2025 Autor: Howard Calhoun | [email protected]. Viimati modifitseeritud: 2025-06-01 07:13
Vaske ja selle sulameid kasutatakse erinevates majandussektorites. See metall on nõudlik selle füüsikalis-keemiliste omaduste tõttu, mis raskendavad ka selle struktuuri töötlemist. Eelkõige nõuab vase keevitamine eritingimusi, kuigi protsess põhineb üsna levinud termilise töötlemise tehnoloogiatel.
Vasest tooriku spetsiifiline keevitamine
Erinev alt paljudest teistest metallidest ja sulamitest iseloomustab vasktooteid kõrge soojusjuhtivus, mistõttu on vaja tõsta keevituskaare soojusvõimsust. Samal ajal on vajalik sümmeetriline soojuse eemaldamine tööpiirkonnast, mis minimeerib defektide tekkimise riski. Teine vase puudus on voolavus. See omadus muutub takistuseks lae ja vertikaalsete õmbluste moodustamisel. Suurte keevisvannidega pole sellised toimingud üldse võimalikud. Isegi väikesed töömahud nõuavad eritingimuste korraldamist grafiidil põhinevate piiravate vooderdiste kasutamisegaja asbest.
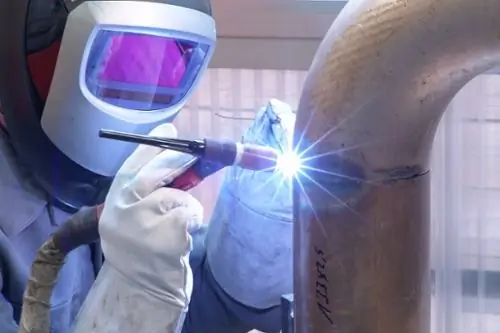
Metalli kalduvus oksüdeeruda nõuab ka spetsiaalsete lisandite, nagu räni-, mangaan- ja fosforgeelide, kasutamist teatud režiimides, kus moodustuvad tulekindlad oksiidid. Vase keevitamise omadused hõlmavad gaaside - näiteks vesiniku ja hapniku - neeldumist. Kui te ei vali termilise kokkupuute optimaalset režiimi, osutub õmblus halva kvaliteediga. Aktiivse koostoime tõttu gaasiga jäävad selle struktuuri suured poorid ja praod.
Vase koostoime lisanditega
On vaja arvestada vase koostoime olemusega erinevate lisandite ja keemiliste elementidega üldiselt, kuna selle metalli keevitamise protsessis kasutatakse sageli erinevatest materjalidest elektroode ja juhtmeid. Näiteks alumiinium võib lahustuda vase sulatis, suurendades selle korrosioonivastaseid omadusi ja vähendades oksüdeeritavust. Berüllium - suurendab mehaanilist takistust, kuid vähendab elektrijuhtivust. Konkreetsed mõjud sõltuvad aga ka kaitsekeskkonna olemusest ja temperatuurirežiimist. Niisiis hõlbustab vase keevitamine 1050 ° C juures rauakomponendi sisenemist tooriku struktuuri koefitsiendiga umbes 3,5%. Kuid umbes 650 ° C režiimis väheneb see näitaja 0,15% -ni. Samal ajal vähendab raud kui selline järsult vase korrosioonikindlust, elektri- ja soojusjuhtivust, kuid suurendab selle tugevust. Metallidest, mis selliseid toorikuid ei mõjuta, võib eristada pliid ja hõbedat.
Põhilised vase keevitusmeetodid
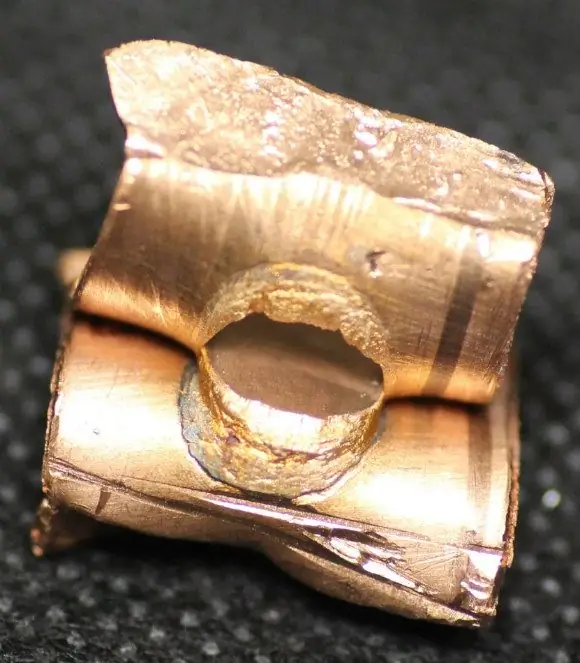
Kõik levinud keevitusmeetodid, sealhulgas käsitsi ja automaatne, on lubatud erinevates konfiguratsioonides. Ühe või teise meetodi valiku määravad ühendusele esitatavad nõuded ja tooriku omadused. Kõige produktiivsemate protsesside hulgas on elektriräbu ja sukelkaarkeevitus. Kui on plaanis saada kvaliteetne õmblus ühe toiminguga, siis on soovitatav pöörduda gaasitehnoloogia poole. Selline lähenemine vase ja selle sulamite keevitamisel madalatel temperatuurigradientidel loob soodsad tingimused tooriku deoksüdatsiooniks ja legeerimiseks. Selle tulemusena on õmblus positiivselt modifitseeritud ja vastupidav. Puhta vase puhul võib kasutada volframelektroodide ja kaitsegaasidega kaarkeevitustehnikaid. Kuid enamasti töötavad nad vase derivaatidega.
Millist varustust kasutatakse?
Vaseeelseid tooteid saab töödelda trei-, lihvimis- ja freespinkidel, et moodustada keevitamiseks mõõtmetega toorikuid. Tööstuses kasutatakse ka plasmakaare lõikamise tehnikat, mis võimaldab lõigata peaaegu täiuslike lõikeservadega. Vase otsekeevitamist teostavad argoonikaare paigaldised, poolautomaatsed seadmed, aga ka inverterseadmed. Seadmete voolutugevus võib olenev alt töödeldava detaili suurusest varieeruda vahemikus 120 kuni 240 A. Elektroodide paksus on tavaliselt 2,5-4 mm - see sõltub jällegi töö keerukusest ja mahust.
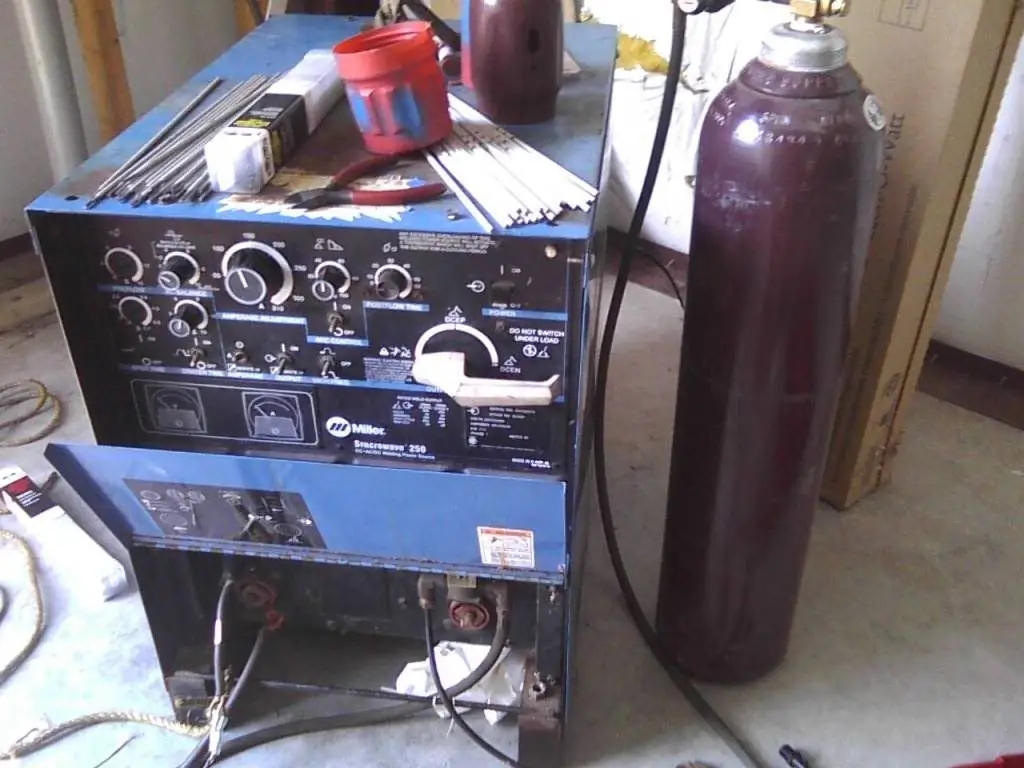
Vakse argoonkeevitus
Üks populaarsemaid meetodeid. Eelkõige kasutatakse mainitud argoon-kaarkeevitamise tehnikat, mis hõlmab volframelektroodide kasutamist. Kuumutamise ajal interakteerub vask hapnikuga, moodustades tooriku pinnale dioksiidi katte. Selles etapis muutub toorik elastseks ja nõuab mittetarbiva elektroodi ühendamist. Näiteks pakuvad kaubamärgi MMZ-2 vardad optimaalset keevituskvaliteeti, kui keevitada vaske kaitsevahendiga argooniga. Kui tooriku tugevat läbitungimist ei seata, võib kasutada lämmastikukeskkonnas keevitamise kerget versiooni. See on hea termilise toime meetod madalal pingel, kuid kombineeritud gaaside abil on võimalik saavutada veelgi suurem mõju keevisõmbluse kvaliteedile. Näiteks kogenud keevitajad kasutavad sageli segusid, mis sisaldavad 75% argooni.
Gaasikeevitus
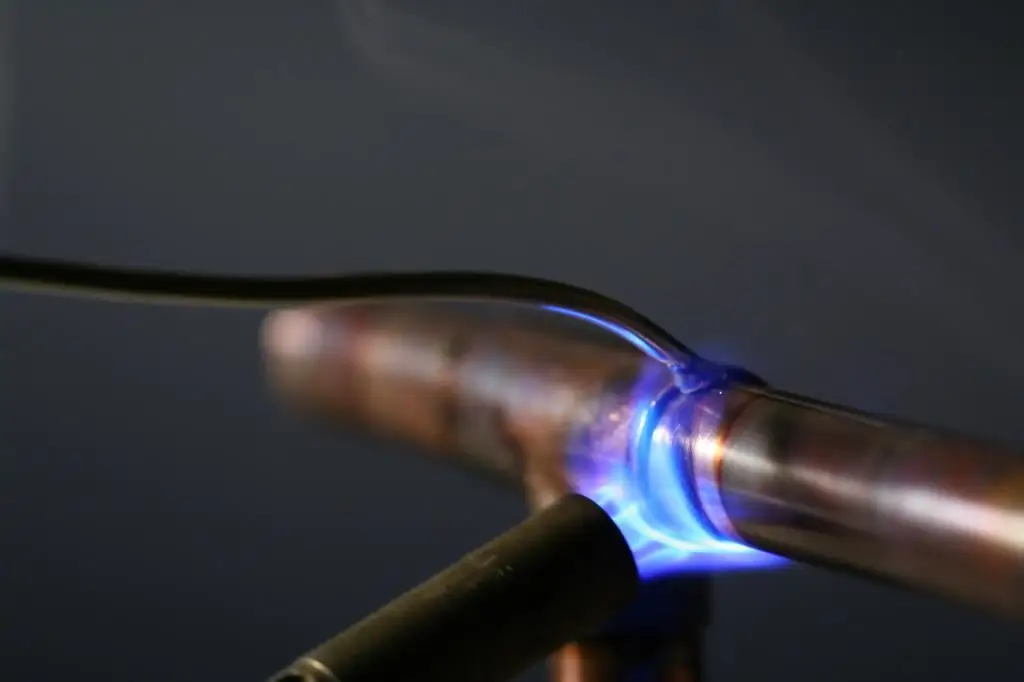
Sel juhul kasutatakse hapniku-atsetüleeni keskkonda, mille tõttu leegi temperatuur tõuseb oluliselt. Tööprotsessis kasutatakse gaasipõletit. See masin on oma jõudluses hea, kuid selle piiratud reguleerimisvõimalused ei võimalda teil keevisvanni parameetreid peenhäälestada.
Sageli kasutatav ja jagatud termilise kokkupuute meetod kahe põleti ühendamisega. Üks on ette nähtud tööpiirkonna soojendamiseks ja teine - otse sihttooriku gaaskeevitamiseks. Seda meetodit soovitatakse kasutada paksude 10 mm lehtede puhul. Kui teist põletit pole,siis saate tulevase õmbluse joonel läbi viia kahepoolse kuumutamise. Efekt ei ole nii kvaliteetne, kuid põhiülesanne on täidetud.
Võimaldab gaaskeevitustehnikat ja räbusti süstimist puhta liitestruktuuri saamiseks. Eelkõige kasutatakse gaasilisi vooge, näiteks boormetüüleetri aseotroopseid lahuseid metüüliga. Selliste segude aktiivsed aurud suunatakse põletisse, muutes keevisvanni omadusi. Leek omandab sel hetkel roheka varjundi.
Süsinikelektroodiga keevitamise omadused
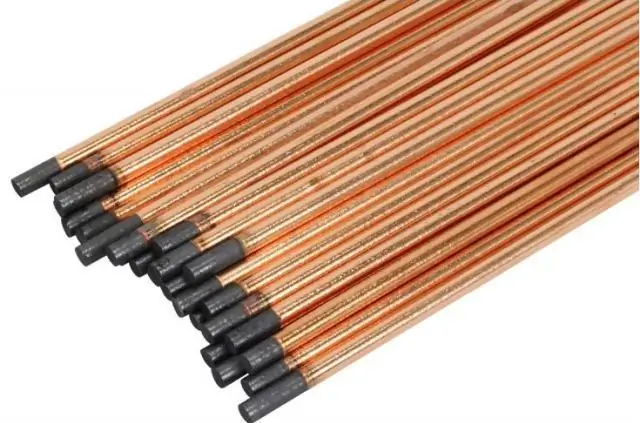
Kaarkeevitusmeetod, mis on optimaalne vasesulamite jaoks. Selle peamist eristavat omadust võib nimetada ergonoomiliseks ja mitmekülgsuseks - vähem alt kõiges, mis on seotud operaatori füüsiliste toimingute tegemise mehaanikaga. Näiteks saab keevitaja teha manipuleerimisi otse õhus, kasutades minimaalset lisakaitsevarustust. See on tingitud asjaolust, et süsinikelektroodid eraldavad kuumutamisel piisavas koguses soojusenergiat, millele keevitatakse väikese võimsusega vask. Protsess osutub ebaefektiivseks, kuid ühendus omandab kõik vajalikud mehaanilised omadused.
Käsitsi kaarkeevitus
Selle keevitusmeetodi tehnoloogia hõlmab kaetud elektroodide kasutamist. See tähendab, et ühendus saab korralikud tugevusomadused, kuid lõppkokkuvõttes erineb toote struktuuri koostis esmasest toorikust. Konkreetsed modifikatsiooniparameetrid määratakse legeerivate deoksüdeerijate omaduste järgi,mis on elektroodi kattekihis. Aktiivkompositsioonis võib kasutada näiteks selliseid komponente nagu madala süsinikusisaldusega ferromangaan, fluoriit, alumiiniumipulber jne. Selline vase keevitamise tehnoloogia ja katete iseseisev tootmine võimaldab. Tavaliselt kasutatakse selleks kuivsegu, mis sõtkutakse vedelas klaasis. Selline kate muudab õmbluse tihedamaks, kuid konstruktsiooni elektrijuhtivus väheneb oluliselt. Üldist kaetud elektroodidega keevitusprotsessi iseloomustab suur pritsmed, mis on vase puhul ebasoovitavad.
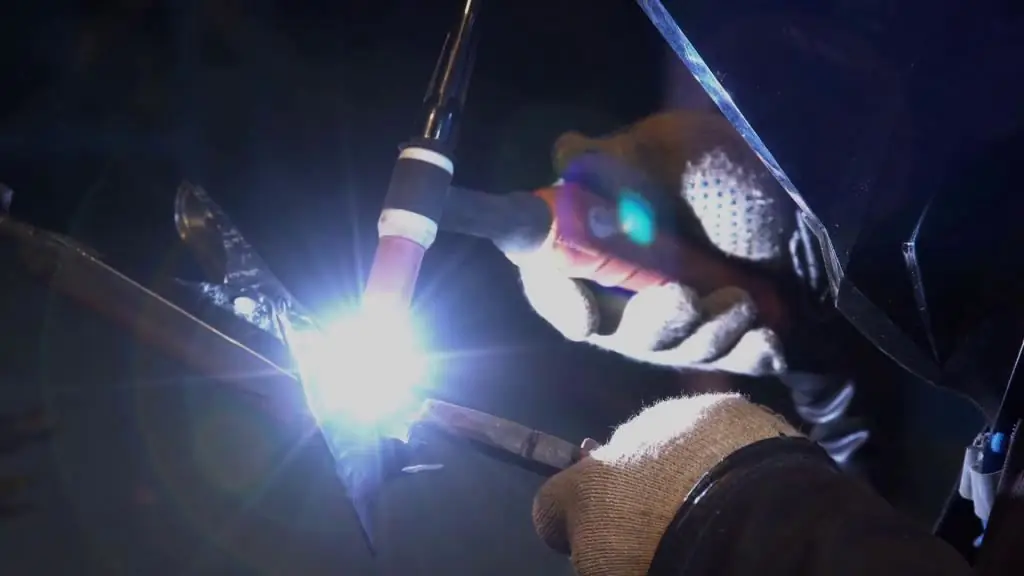
Sukelkaarkeevitus
Räbusti ise vasega keevitamiseks on vajalik kaare stabilisaatorina ja, mis kõige tähtsam, kaitsebarjäärina atmosfääriõhu negatiivsete mõjude eest. Protsessi korraldamisel kasutatakse mittetarbitavaid grafiit- või süsinikelektroode, aga ka kuluvaid vardaid keraamilise voo all. Kui kasutatakse süsinikku, teritatakse vase keevitamiseks mõeldud elektroodid, et moodustada spaatli kujuline lame ots. Tööpiirkonda tarnitakse küljelt ka tobakist või messingist täitematerjal - see on vajalik õmbluse struktuuri deoksüdeerimiseks.
Toiming teostatakse alalisvoolul koos kuumutamisega. Mitmed kaitsetõkked säilitavad tooriku põhistruktuuri, kuigi enamasti püüavad kogenud keevitajad parandada materjali koostist legeeritud traadiga. Jällegi, soovimatute sulavoogude vältimiseks on soovitatav esialgu varustada grafiidist substraat,mis toimib ka voo vormina. Selle meetodi optimaalne töötemperatuur on 300-400 °C.
Kaarkeevitus
Keevitusüritused inverterite ja muude poolautomaatsete seadmete ühendamisega viiakse läbi traadi etteandega gaasilises keskkonnas. Sel juhul saab lisaks argoonile ja lämmastikule kasutada heeliumi, aga ka erinevaid gaasisegude kombinatsioone. Selle tehnika eelised hõlmavad võimalust tungida tõhus alt läbi paksude toorikute, säilitades kõrgel tasemel tooriku mehaanilised omadused.
Võimas termiline efekt on seletatav ülitõhusate plasmavoogudega põlevas gaasilises keskkonnas, kuid need parameetrid määravad ka konkreetse inverteri mudeli omadused. Samal ajal on 1-2 mm paksuste detailide puhul eelistatavam vase argoon-kaarkeevitamise tehnika. Mis puutub gaasilise keskkonna kaitsefunktsiooni, siis sellele ei saa täielikult loota. Jätkub oksiidide, poorsuse ja traadi lisandite negatiivse mõju oht. Teisest küljest kaitseb argooni keskkond tõhus alt töödeldavat detaili õhu hapnikuga kokkupuute eest.
Järeldus
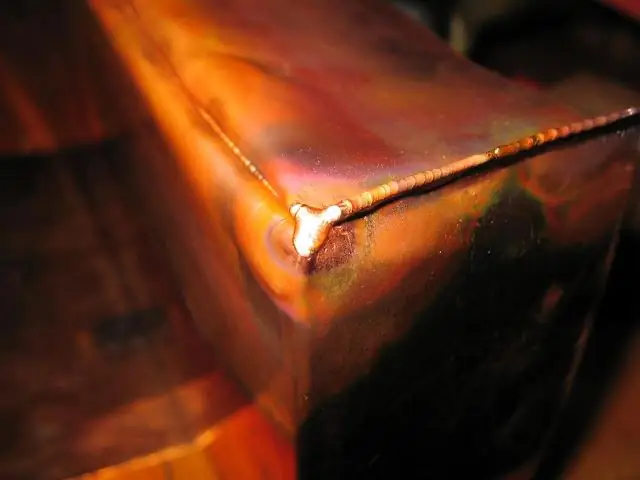
Vasel on palju omadusi, mis eristavad seda teistest metallidest. Kuid isegi selle sulamite üldises rühmas on palju erinevusi, mis nõuavad igal juhul individuaalse lähenemisviisi otsimist õmbluse moodustamise optimaalse tehnoloogia valimiseks. Näiteks gaaskeevitus sobib juhtudel, kui on vaja saada tugev ühendus suures toorikus. Küll aga uued tulijadseda meetodit ei soovitata kõrgete ohutusnõuete tõttu põletite ja gaasiballoonidega töötamisel. Suure täpsusega väikeseformaadilised keevitustööd on usaldatud mugavatele ja tootlikele poolautomaatidele. Selliste seadmetega saab hakkama ka kogenematu operaator, kes kontrollib täielikult töövoo parameetreid. Ärge unustage gaasilise keskkonna tähtsust. Neid saab kasutada mitte ainult tooriku isolaatorina keevitamise ajal, vaid ka võimalusena parandada mõningaid materjali tehnilisi ja füüsikalisi omadusi. Sama kehtib elektroodide kohta, mis võivad anda positiivse legeerefekti.
Soovitan:
Mineraalide rikastamine: põhimeetodid, tehnoloogiad ja seadmed
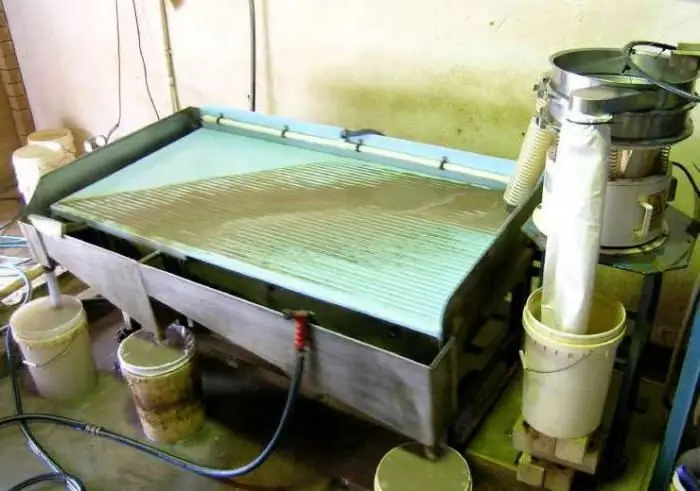
Artikkel on pühendatud mineraalide töötlemise tehnoloogiale. Kirjeldatakse sellise töötlemise etappe ja meetodeid
Alumiiniumi ja selle sulamite korrosioon. Alumiiniumi korrosioonivastase võitluse ja selle kaitsmise meetodid
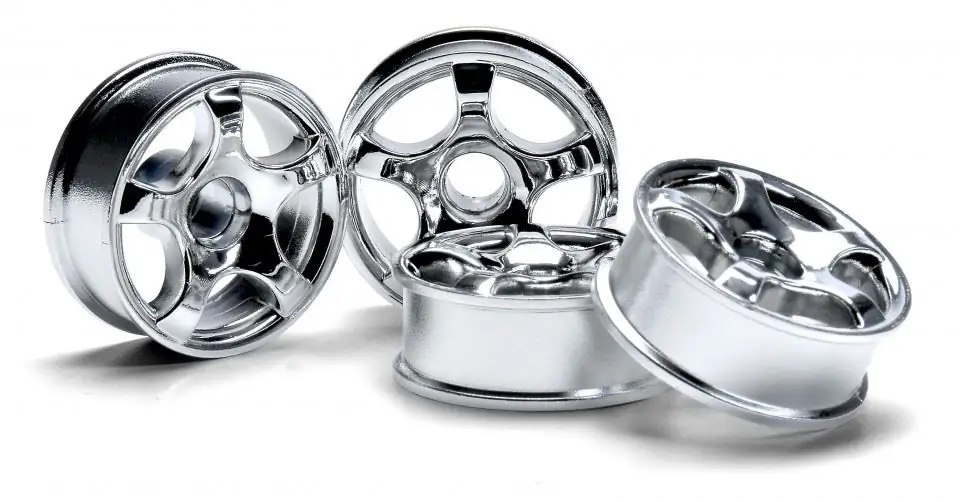
Alumiinium on erinev alt rauast ja terasest üsna korrosioonikindel. Seda metalli kaitseb rooste eest selle pinnale moodustunud tihe oksiidkile. Viimase hävitamise korral aga suureneb alumiiniumi keemiline aktiivsus tunduv alt
Vase ja selle sulamite korrosioon: põhjused ja lahendused
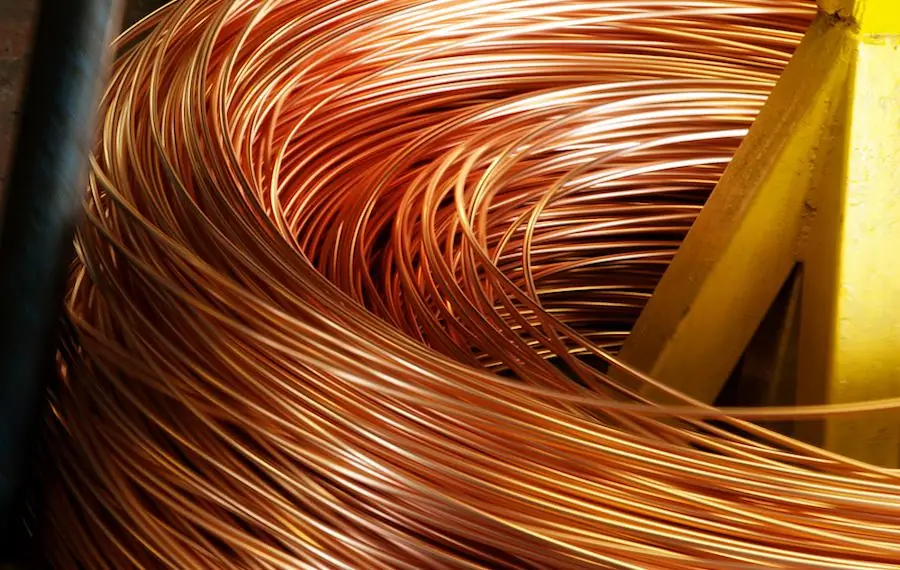
Vasel ja vasesulamitel on kõrge elektri- ja soojusjuhtivus, neid saab töödelda, neil on hea korrosioonikindlus, seetõttu kasutatakse neid aktiivselt paljudes tööstusharudes. Kuid kui see satub teatud keskkonda, avaldub vase ja selle sulamite korrosioon ikkagi. Mis see on ja kuidas tooteid kahjustuste eest kaitsta, käsitleme selles artiklis
Kuidas isekeermestavaid kruvisid tehases valmistatakse: tehnoloogiad ja seadmed. Masin isekeermestavate kruvide tootmiseks
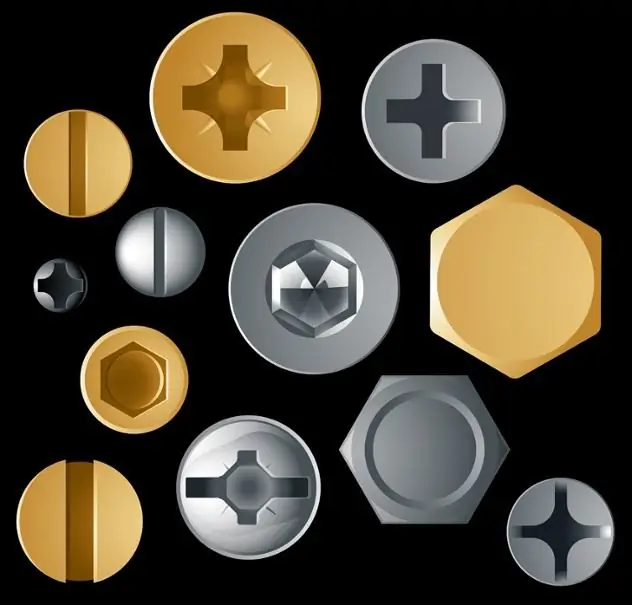
Kuidas valmistatakse isekeermestavaid kruvisid tehases? Vastus sellele küsimusele on üsna lihtne tehnoloogia. Ettevõtetes valmistatakse mütsidega toorikud esm alt terastraadist. Lisaks lõigatakse sellistele toorikutele niidid
Ultraheliplastide, plastide, metallide, polümeermaterjalide, alumiiniumprofiilide keevitamine. Ultraheli keevitamine: tehnoloogia, kahjulikud tegurid
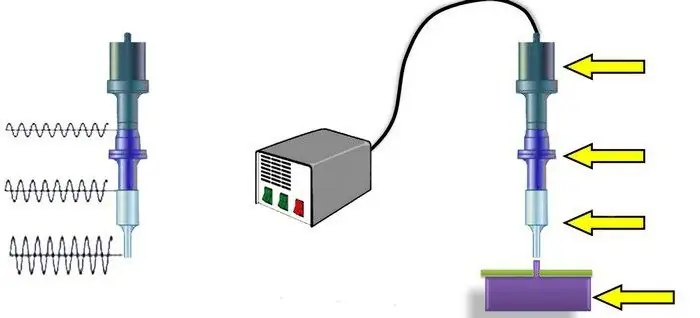
Metallide ultrahelikeevitus on protsess, mille käigus saadakse püsiv ühendus tahkes faasis. Noorte alade moodustumine (milles tekivad sidemed) ja nendevaheline kontakt toimub spetsiaalse tööriista mõjul