2025 Autor: Howard Calhoun | [email protected]. Viimati modifitseeritud: 2025-06-01 07:13
Ajalise koksistamise seadmed on raskeõli rafineerimise kõige levinum riistvaralahendus. Nende seade sisaldab 2 põhimoodulit - reaktorit, kus toormaterjali kuumutatakse ja koksitakse ning mehaaniline töötlemine. Tehaste projekteerimine toimub etapiviisiliselt ja hõlmab protsessiseadmete arvutamist ja valikut, tehniliste ja majanduslike näitajate määramist.
Sihtkoht
Koksimise tehnoloogiline protsess on üks nafta rafineerimise viise. Selle põhieesmärk on saada suurt tükki sisaldavat naftakoksi. Tööstuses kasutatakse kolme koksistamise meetodit:
- Perioodiline, kuubik. Tooraine laaditakse horisontaalsesse aparaati, kuumutatakse selle all oleva kaminaga, seejärel k altsineeritakse 2-3 tundi. Pärast seda ahi jahutatakse ja valmistoode laaditakse maha. See meetod on kõige lihtsam ja vähem tootlik.
- Pidev. See meetod on veel tööstuse arengujärgus.
- Poolpidev, praegu vastu võetudkõige levinum.
Ultraviivitusega koksimisseadmed on uusimat tüüpi protsessiseadmed. Nendes eelkuumutatakse tooraine ahjus ja viiakse seejärel kuumutamata reaktsioonikambritesse, millel on vajaliku temperatuuri säilitamiseks soojusisolatsioonikiht. Reaktorite arv ja suurus, ahjude võimsus mõjutavad kogu jaama jõudlust.
Esimese DCU tööd Venemaal alustati 1965. aastal Ufaneftekhimis. Tehase hiline koksiseade töötab tänaseni. Pärast 2007. aasta rekonstrueerimist on selle tootlikkus töödeldud tooraine massist 700-750 tuhat tonni aastas.
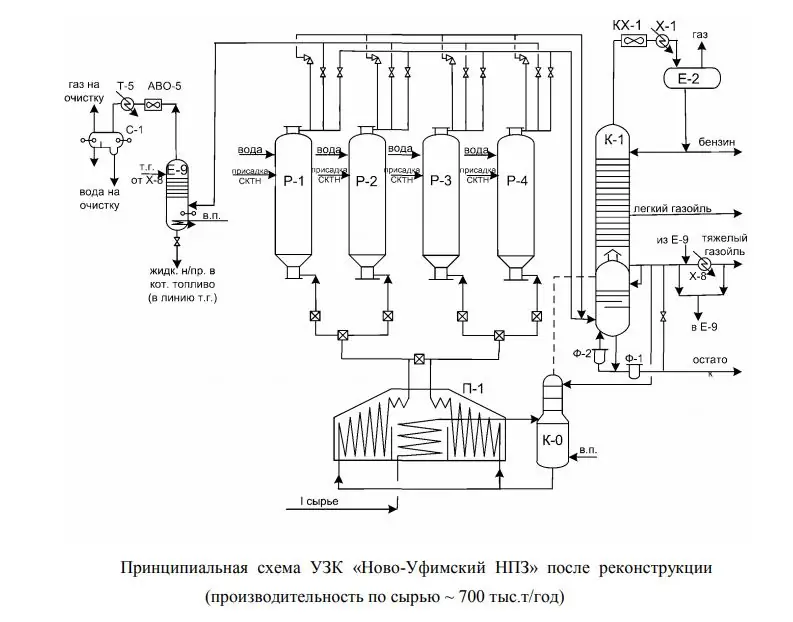
Lõpptooted
Ultraheli testimisel saadakse järgmisi aineid, välja arvatud koks:
- koksimisgaasid (kasutatakse protsessikütusena või töödeldakse propaan-butaani fraktsiooni saamiseks);
- bensiin;
- koksi destillaadid (kütus, krakkimise lähteaine).
Kodumaistel ultraheli testimismasinatel on koksi saagis 20-30 massiprotsenti. See näitaja sõltub eelkõige tooraine kvaliteedist. Metallurgiatööstuses on selle toote järele kõige suurem vajadus (anoodide ja elektroodide, alumiiniumi, abrasiivide, karbiidide, süsinik-grafiitmaterjalide, ferrosulamite tootmine). Lisaks esimesele Ufa DCU-le on Venemaal ehitatud ka teisi viivitusega koksiseadmeid: Omski rafineerimistehases, Novokuibõševski rafineerimistehases, LLC LUKOIL-Volgogradneftepererabotka, LUKOIL-Permnefteorgsintez, LUKOIL-Permnefteorgsintez, Angarski naftakeemiaettevõte, NOVOIL OJSC (Ufa), TANECO PJSC (Nižnekamsk).
Tooraine
Koksimiseks kasutatavad toiduained jagunevad 2 rühma: esmase ja sekundaarse töötlemise tooted. Hilise koksistamise seadmetes kasutatakse toorainena järgmisi aineid:
- kütteõli;
- pooltõrva;
- tar;
- söetõrva pigi;
- asf alt ja muud tööstuslikud naftatooted;
- vedel kivisöe jääk;
- raske pürolüüs ja põlevkivitõrv;
- termilise pragunemise jäägid;
- naftabituumen ja rasked õlid.
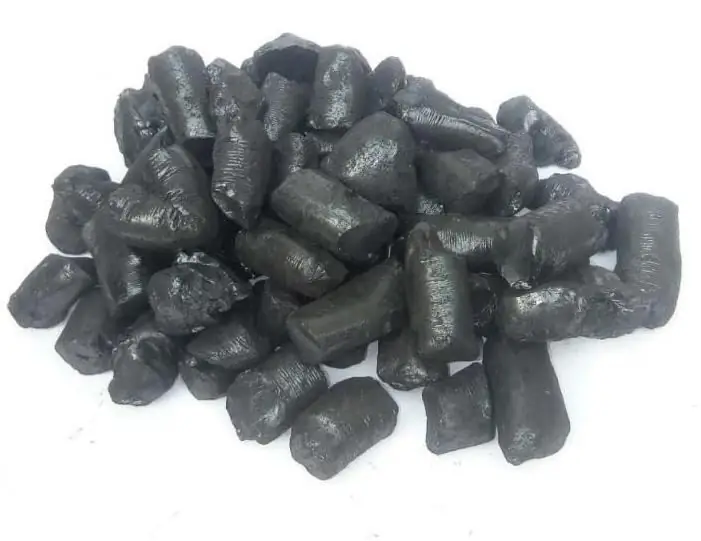
Kõrgelt aromatiseeritud õlijäägid on praegu kõige levinum lähteaine.
Mõju tehnoloogilistele parameetritele
Koksimistehase järgmised parameetrid sõltuvad söödamaterjali omadustest:
- reaktsioonikambri efektiivsus;
- saadud toodete kvaliteet;
- koksi müügikoht;
- protsessi tingimused.
Kõige olulisemad tooraine parameetrid on:
- Koksimine, olenev alt asf altvaiguainete sisaldusest. Koksimisväärtus peaks jääma vahemikku 10-20%. Väiksema väärtuse korral koksi saagis väheneb ja suurema puhul kogunevad ahjudesse mähiste sisse sademed. Koksimisvõime määratakse tiiglis oleva tahke jäägi massi järgi pärast selles oleva naftasaaduse proovi kuumutamist.
- Tihedus.
- Keemiline koostis. Alateskahjulikud lisandid, millel on suurim mõju koksi kvaliteedile, eraldavad väävlit (seda ei tohiks olla rohkem kui 1,5 massiprotsenti). Sõltuv alt koksi otstarbest tehnoloogilises protsessis on eelistatav kasutada erinevat tüüpi toorainet. Seega kasutatakse lõpptoote kiulise struktuuri saamiseks parafiinipõhiseid materjale.
Koksi saagis on võrdeline sööda tiheduse ja asf alteenisisaldusega.
Koksimisetapid
Tehnoloogiline protsess viivitusega koksiseadmetes on pikk ja pidev, alates tooraine tarnimisest kuni valmistoote mahalaadimiseni. Tavaliselt jaguneb see kolmeks etapiks:
- Lagunemisreaktsioonid, destillaadi fraktsioonide moodustumine, vaheühendid, kondenseerumine.
- Küllastumata süsivesinike sisalduse märkimisväärne vähenemine gaasides, jääkkomponentide molekulmassi suurenemine, tsükliseerimisreaktsioonid.
- Asf alteenide sisalduse suurenemine jäägis kuni 26%, vaikude ja õlide koguse vähendamine. Teisendage vedel jääk tahkeks koksiks.
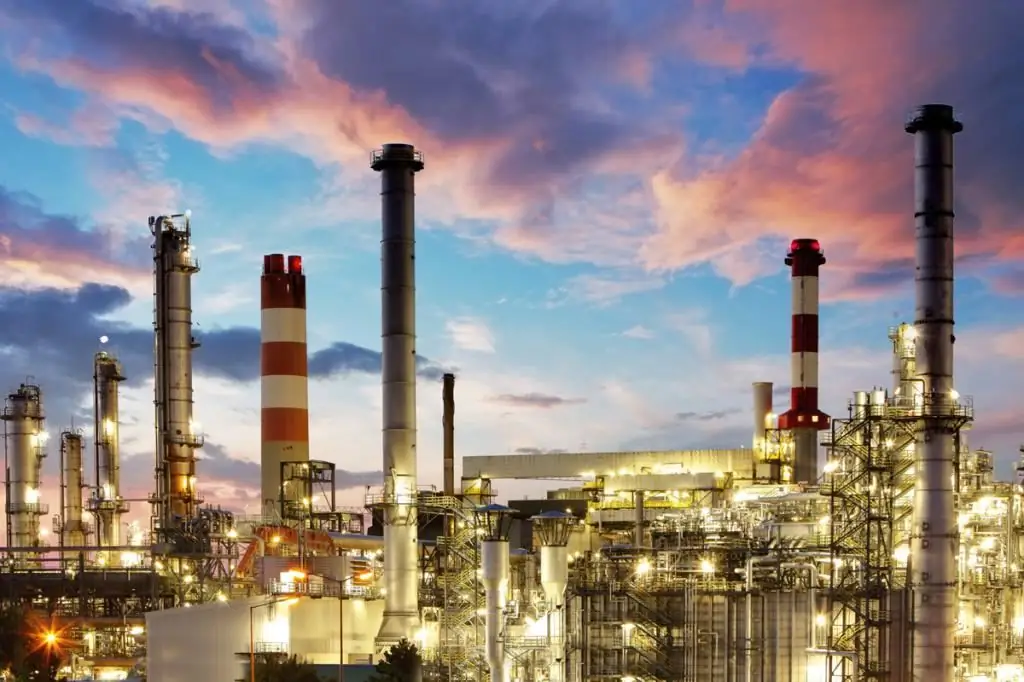
Klassifikatsioon
Sõltuv alt nende paigutusest on 2 peamist viivitusega koksistamise ühikut: üheplokilised ja topeltplokid.
Kaheplokiliste tehaste hulgas on 4 tüüpi, mida iseloomustavad järgmised disaini- ja tehnoloogilised omadused:
- Koksimiskambrite siseläbimõõt - 4,6 m Telkkütte ahjud, neli paarikaupa töötavat kambrit. Kütmiseks kasutatakse koksistamise käigus saadud petrooleumi ja gaasiõli.
- Kokskambrid Ø 5,5 m. Lähteaine - otsedestillatsiooniga kütteõlid väga aromaatsete süsivesinike lisamisega, mis suurendavad kvaliteetse toote saagist.
- Leegeeritud terasest reaktorid Ø 5,5 m, kõrgus 27,6 m, mahulise põletiga toruahjud, suurendatud ristlõikega õhuklapid, radioaktiivsed tasememõõturid, mis võimaldavad registreerida koksi-vahu faasieralduse asukohta. Uusim uuendus aitab paremini ära kasutada reaktori kasulikku mahtu. Turbulaatorite tarnimine puhastuslisanditega, mis vähendavad spiraalide koksimist, jahutatud gaasiõli peatorudes.
- Reaktsioonikambrid Ø 7 m, kõrgus 29,3 m Tooraine aksiaalne sisend reaktoritesse, hüdraulikasüsteem koksi väljajuhtimiseks puldiga, elektrikraanad, laod põrandatüüpi ladudega.
Rakendusseadmed
Seda tüüpi paigaldistega varustatud seadmed jagunevad olenev alt eesmärgist järgmistesse rühmadesse:
- Tehnoloogiline, otseselt seotud koksistamise protsessiga (ahjud, kolonniseadmed, soojusvahetid, reaktorikambrid, kuubikud, külmikud, pumbad, torustikud, mõõteriistad, kraanid ja muud sulge- ja lülitusventiilid).
- Reovesi - vee kogumine ja töötlemine töötsüklisse naasmiseks (jahutus- ja koksi ekstraheerimine).
- Seadmed koksi kambritest (kuubikutest) mahalaadimiseks. Kaasaegsetes mehhaniseeritud paigaldistes võib see olla mehaanilist ja hüdraulilist tüüpi (tropid, vintsid, kammid, lõikurid, vardad, tornid, kummist hülsid).
- Seadmed valmistoote transportimiseks ja töötlemiseks (vastuvõturennid ja kaldteed, kraanad, konveierid, söötjad, purustid, laod).
- Masinad ja seadmed töö mehhaniseerimiseks.
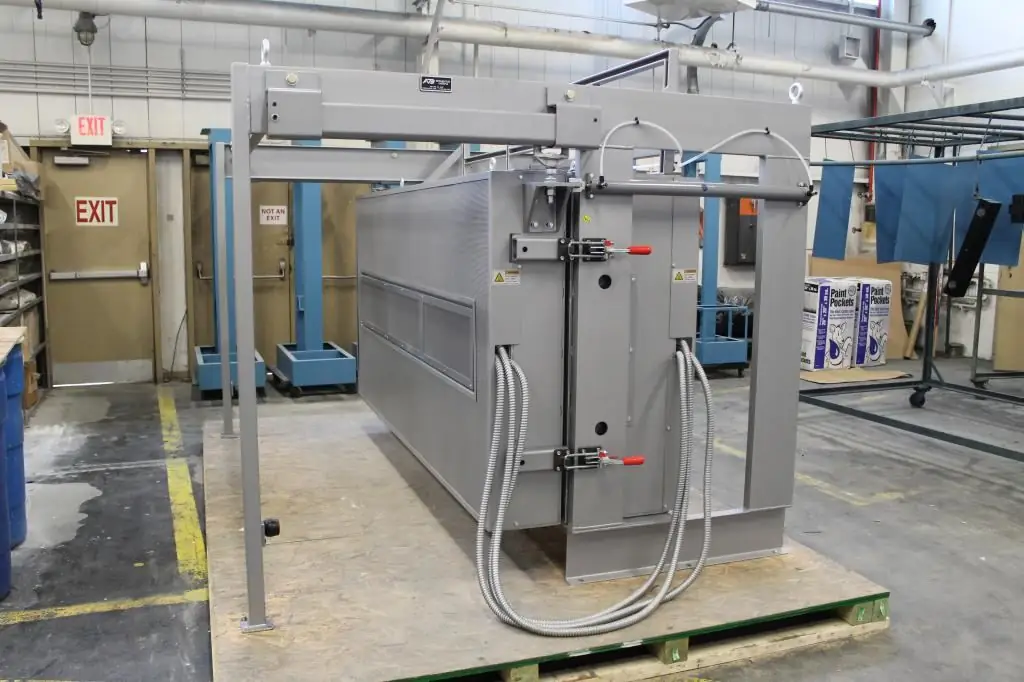
Ajalise koksistamise tehaste projekteerimisel tuleb hoolik alt läbi mõelda reaktsioonikambrite ja ahjude konstruktsioon, kuna töötsükli kestus sõltub nende töökindlusest.
Protsessi parameetrid
Koksimistehnoloogia peamised parameetrid on:
- Retsirkulatsiooni suhe, mis on defineeritud kui ahjude reaktsioonipoolide kogukoormuse ja kogu seadme koormuse suhe toorainena. Selle väärtuse kasvades suureneb kvaliteetse koksi, gaasi ja bensiini saagis, kuid raske gaasiõli kogus väheneb.
- Rõhk reaktsioonikambris. Selle vähenemine toob kaasa gaasiõli saagise suurenemise, koksi ja gaasi saagise vähenemise ning vahutamise suurenemise.
- Protsessi temperatuur. Mida suurem see on, seda kõrgem on koksi kvaliteet lenduvate ainete koguse, tugevuse ja tiheduse poolest. Maksimaalset väärtust piirab ahju ja torustike koksistumise oht, mis vähendab mähiste vastupidavust. Igal tooraineliigil on oma optimaalne temperatuur.
Hilinenud koksiseadmete ehitamine on seotud suurte kapitalikuludega. Seetõttu tehakse enamasti juba toimiva seadmete kompleksi rekonstrueerimine. See saavutatakse tsükli vähendamisegakoksistamine, uute reaktsioonikambrite kasutuselevõtt või retsirkulatsiooni suhte vähendamine.
Tööpõhimõte
Ajaga koksistamise seadmed koosnevad ühest või mitmest paaris kambrirühmast, milles üks kamber töötab koksi tootmise etapis ja teine mahalaadimisel või vahepealses olekus. Lähtematerjali lagunemisprotsess algab toruahjus, kus see kuumutatakse temperatuurini 470-510 °C. Pärast seda siseneb tooraine kütmata kambritesse, kus see kaasnenud kuumuse tõttu sügav alt koksiseerub.
Gaasilised ja vedelad süsivesinikud eraldatakse fraktsioneerivaks eraldamiseks destilleerimiskolonnis. Koks jõuab mehaanilise töötlemise osakonda, kus see maha laaditakse, sorteeritakse ja transporditakse. Valmistoote kihti puuritakse kaev, millesse asetatakse hüdrauliline lõikur. Selle düüsid töötavad rõhu all kuni 20 MPa. Eraldatud koksi tükid kukuvad äravooluplatvormile, kus vesi tühjendatakse. Seejärel purustatakse toode väiksemateks tükkideks ja jagatakse fraktsioonideks. Järgmiseks viiakse koks lattu.
Ultraheli põhimõtteline diagramm on näidatud alloleval joonisel.
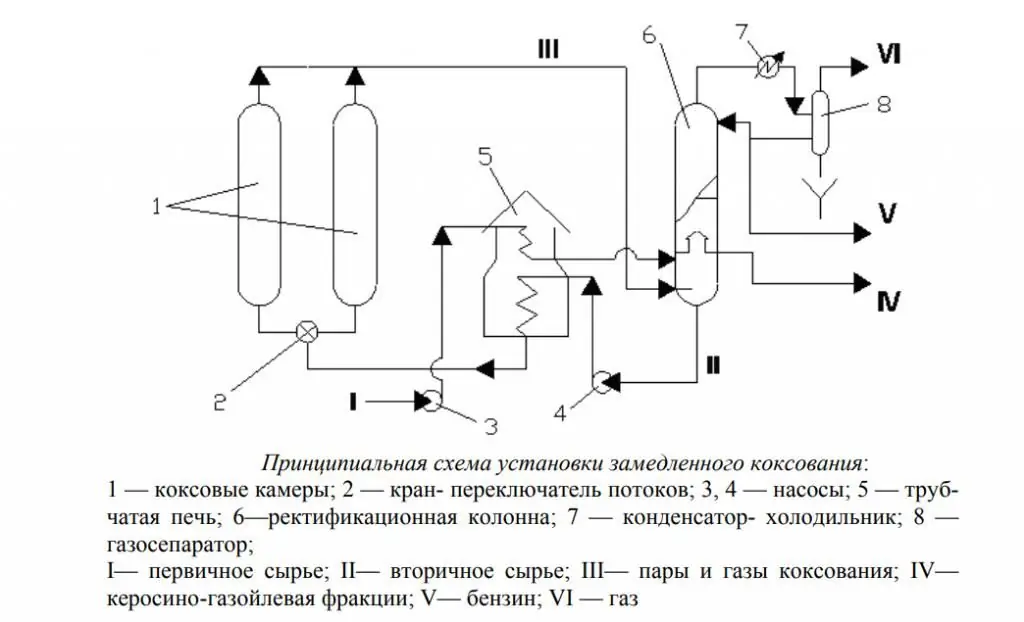
Koksikambrid
Kambrid on reaktor, mis on kogu paigalduse aluseks. Kambri töötsükkel on tavaliselt 48 tundi, kuid viimastel aastatel on konstrueeritud 18- ja 36-tunnises režiimis töötavad ultraheliseadmed.
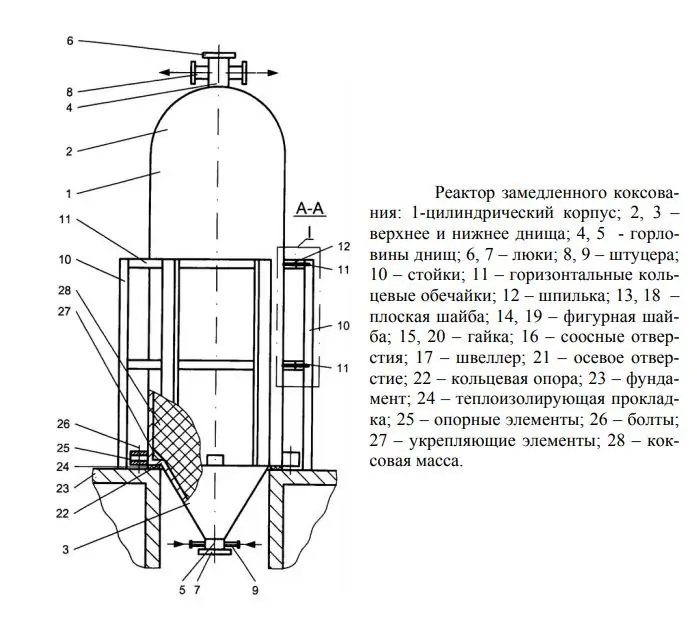
Üks reaktori töötsükkel koosneb järgmistest toimingutest:
- tooraine laadimine, koksimise protsess (1 päev);
- off (1/2 tundi);
- hüdrotermiline ravi (2,5 tundi);
- toote vesijahutus, vee eemaldamine (4 tundi);
- toode mahalaadimine (5 tundi);
- kaevude tihendamine, survekatse kuuma auruga (2 tundi);
- küte õliaurudega, lülitumine töötsüklile (3 tundi).
Disain
Ajaline koksiseadme projekt töötatakse välja järgmises järjekorras:
- nõutava tootlikkuse määramine, t/aastas;
- ressursibaasi analüüs;
- koksimisprotsessi teoreetilise materjalibilansi koostamine eri tüüpi toorainete jaoks;
- peamiste materjalivoogude määramine;
- paigalduskontseptsiooni väljatöötamine;
- reaktorite suuruse ja arvu põhjendus;
- ühe kambri koksiga täitmise kestuse määramine ja selle hüdrauliline arvutus, reaktori töögraafiku koostamine;
- kambri temperatuurikoormuse arvutused;
- konvektsiooni- ja kiirguskambrite arvutamine;
- tootmisliini paigutuse arendamine;
- muude põhiseadmete (destilleerimiskolonn, ahjud, külmikud jne) tehnoloogilised arvutused;
- seire- ja juhtimissüsteemi arendamine, automatiseerimisvahendite valik;
- hädakaitseskeemide kirjeldus;
- keskkonnaaspektide ja ohutusmeetmete arendamine;
- majandusnäitajate määramine (kapitalikulud, teenindava personali arv, palgafond,tooraine ja abimaterjalide tootmiskulud, aastane majanduslik efekt, toote maksumus).
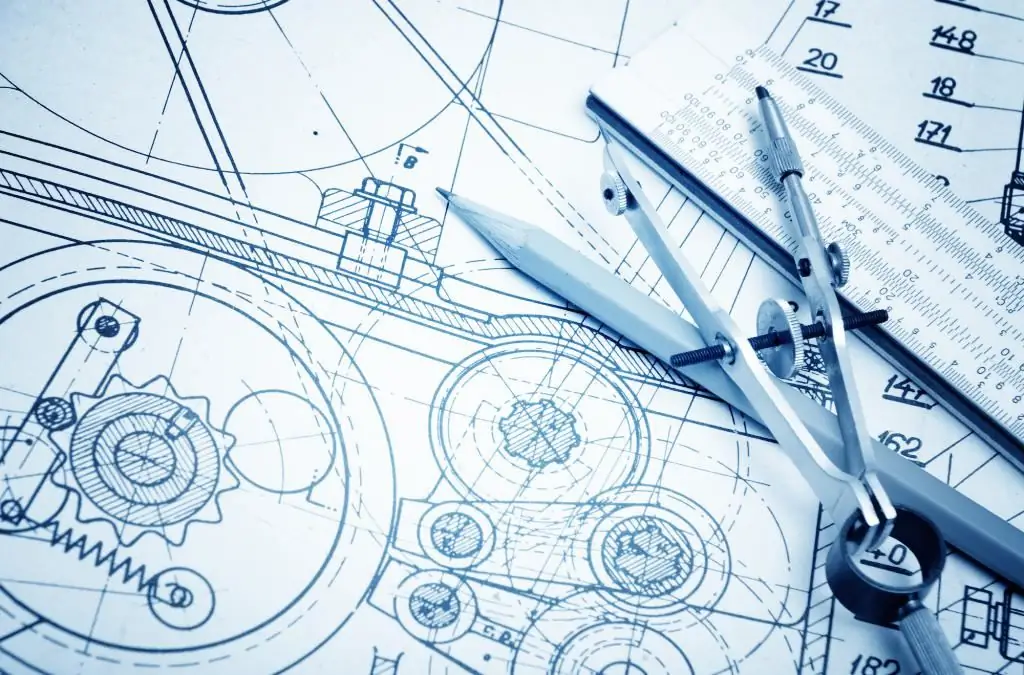
Ajastatud koksistamise agregaadi võimsuse aastane arvutamine toimub järgmise valemi järgi:
N=P x t, kus P on tehase võimsus, t/päevas;
t on tööpäevade arv aastas.
Toote toodang füüsilises mõttes vastav alt põhi- ja konstruktsioonivalikutele määratakse paigaldise materjalibilansi alusel.
Soovitan:
Tööstuse tooraine - valge kvartsliiv
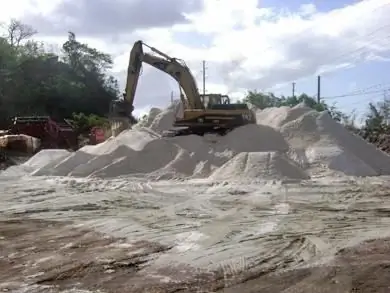
Milliseid imesid pole Maal inimese jaoks ette valmistatud! Siin on näiteks hämmastav vaatepilt – valge liiv. Kaugelt vaadates ei saa kohe aru: kas lumehanged keset suve või granuleeritud suhkru mäed või lauasool või mõni muu kemikaal?
Rõivatööstus kui kergetööstuse haru. Rõivatööstuse tehnoloogiad, seadmed ja tooraine
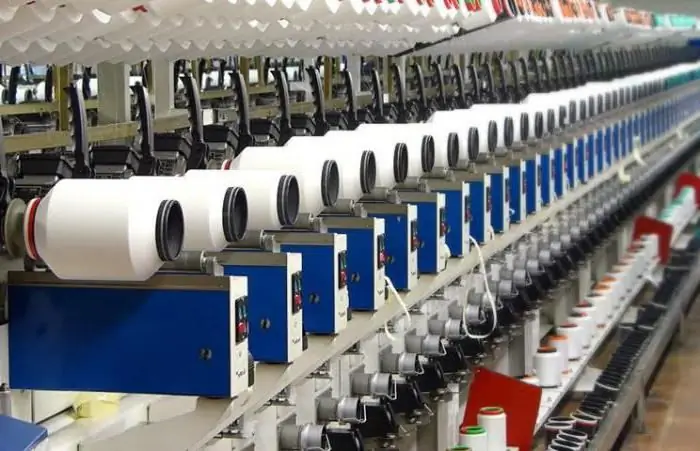
Artikkel on pühendatud rõivatööstusele. Arvesse võetakse selles tööstusharus kasutatavaid tehnoloogiaid, seadmeid, toorainet jne
Tooraine on tootmise aluseks
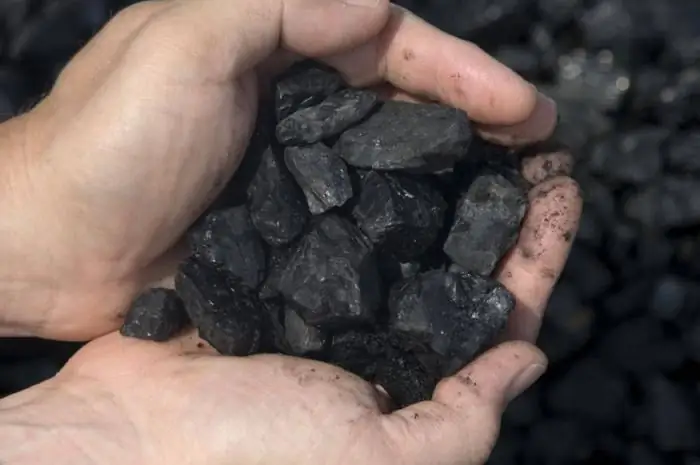
Tooraine on materjal, mis on ette nähtud tootmises edasiseks töötlemiseks. Tegelikult algab iga toote väljalaskmine temaga
Kvassi tootmine: vajalikud seadmed, tooraine ja retseptid
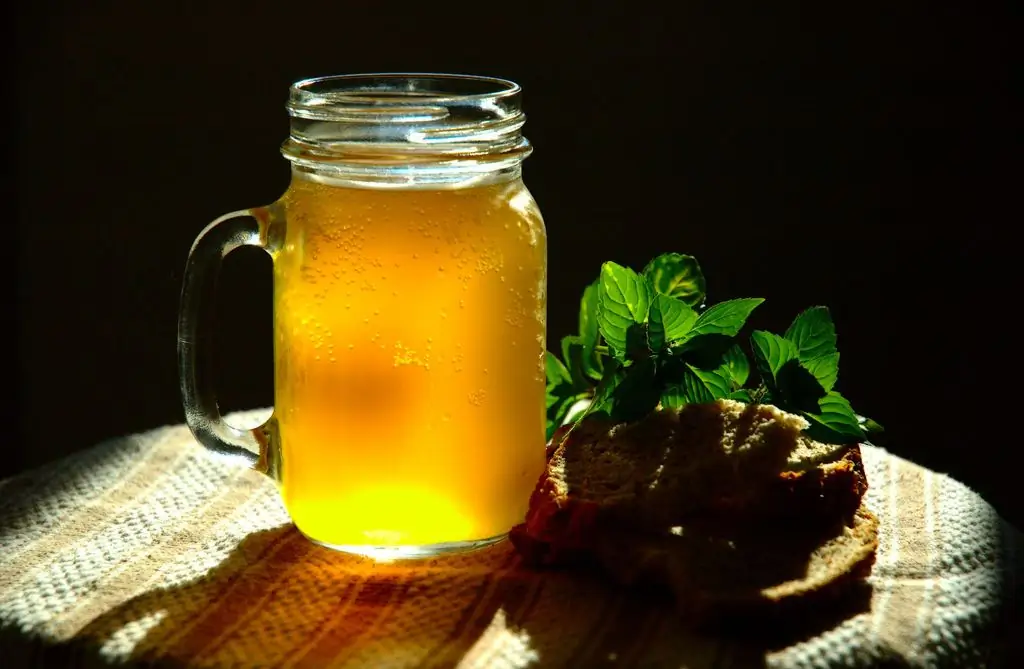
Eluskalja tootmise ja turustamise omadused. Kodune või tööstuslik tootmine. Ruumide ja põhivarustuse valik olenev alt joogi valmistamise eeldatavast mahust. Tehases tootmise tehnoloogiline protsess. Näited retseptidest koduseks või väiketootmiseks
Vene Föderatsiooni strateegiline looduslik tooraine - nafta "Uurals"
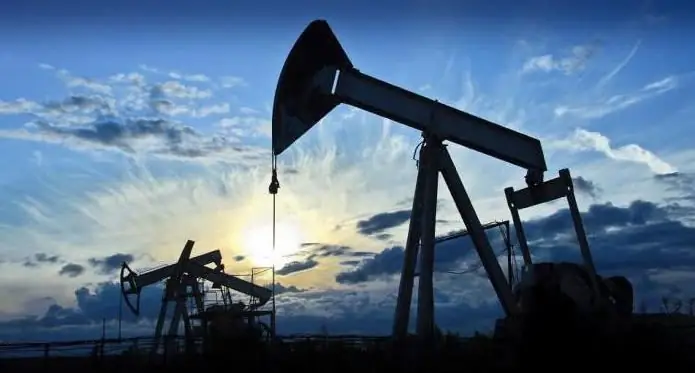
Uurali nafta on Venemaa süsivesinike peamine ekspordiliik. Riigi eelarve sõltub otseselt selle kaubamärgi naftast, kuna see arvutatakse majandusteadlaste praeguste prognooside kohaselt tooraine maksumuse alusel