2025 Autor: Howard Calhoun | [email protected]. Viimati modifitseeritud: 2025-06-01 07:13
Lämmastikhape on üks enim nõutud tööstusliku tooraine liike. Selle tootmine võib toimuda erinevate meetoditega - olenev alt sordist, milles hapet kliendile tarnida. Mis on asjakohaste tehnoloogiate olemus? Kuidas neid võrrelda tehases toodetud lämmastikhappe tüübiga?
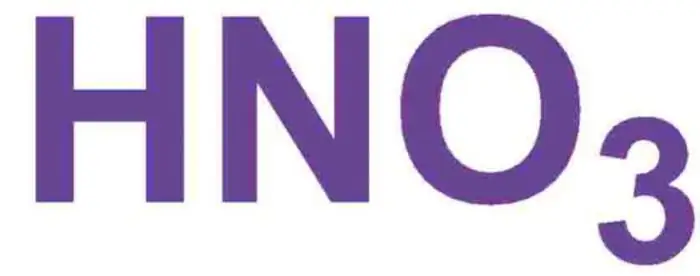
Lämmastikhappe tööstuslik tootmine: tehnoloogia arengu ajalugu
Kõigepe alt on kasulik uurida ajaloolisi fakte selle kohta, kuidas lämmastikhappe tootmine Venemaal arenes. Kodumaises tööstuses algatati selle aine vabastamine olemasoleva teabe kohaselt Peeter I juhtimisel. Seejärel pakkus M. V. Lomonosov välja meetodi salpeetrist lämmastikhappe tootmiseks - seda ainet peeti tegelikult tootmise peamiseks tooraineks. kõnealusest ainest kuni 20. sajandi alguseni.
Lisaks soolapeetriga kasutati väävelhapet ka lämmastikhappe tootmisel tööstuses. Kaks vaadeldavat ainet moodustasid üksteisega suhtlemisel lämmastikhappe ja naatriumvääveloksiidi. Selle eelismeetod oli võime saada lämmastikhapet kontsentratsiooniga umbes 96-98% (tingimusel, et kasutatakse nõutava kvaliteediga toorainet).
Aktiivselt on täiustatud vastavat tehnoloogiat - toorme töötlemise kiiruse suurendamise ja suurema koguse toote väljundi tagamise kasuks. Kuid järk-järgult andis see teed kontseptsioonile, et lämmastikhappe tootmine viidi läbi ammoniaagi kontaktoksüdatsiooni teel.
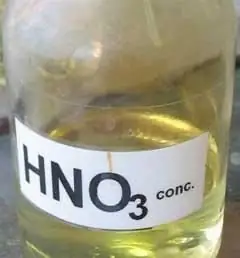
Samuti leiutati meetod, mille kohaselt kasutati happe tootmise peamise toorainena lämmastikoksiidi, mis saadi atmosfäärist vastava gaasi kaaroksüdeerimisel. On lai alt levinud seisukoht, et esimene meetod on kuluefektiivsem.
Lämmastikhappe tootmise tehnoloogiliste lähenemiste täiustamisel on kujunenud lähenemine, mille kohaselt on vastava aine tootmiseks optimaalseim variant kõrgsurve all töötava tööstusliku infrastruktuuri kasutamine. Selle alternatiiviks on happe tootmine atmosfäärirõhul, mida peetakse majanduslikust seisukohast vähem tulusaks.
Aine vabanemine normaalsel või kõrgendatud rõhul hõlmab lämmastikhappe tootmist ammoniaagist. Samuti on kombineeritud meetod, mis ühendab kahe teise eelised. Lämmastikhappe kombineeritud meetodil tootmise tunnused on esiteks ammoniaagi oksüdeerimine atmosfäärirõhul ja selle imendumine - temperatuurilsuurenenud.
Ammoniaaki peetakse nüüd koos vee ja atmosfääriõhuga kõnealuse aine eraldumise peamiseks tooraineks. Uurime lähem alt nende kasutamise eripärasid happe tootmisel.
Lämmastikhappe lähteaine
Niisiis on kõnealuse aine tootmisel kasutatavad peamised toorained ammoniaak, õhk ja ka vesi.
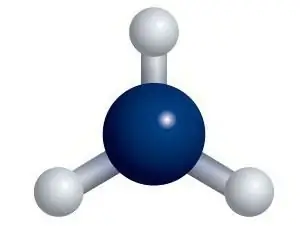
See nõuab puhastatud ammoniaagi kasutamist. Selleks puhastatakse seda spetsiaalsetes aurustus- ja destilleerimisseadmetes erinevate tootmistsüklite raames. Samamoodi tuleb lämmastikhappe väljalaskmisel kasutada puhast õhku. Samuti filtreeritakse spetsiaalse varustuse abil. Lämmastikhappe tootmisel kasutatav vesi omakorda puhastatakse lisanditest ja sooladest. Paljudel juhtudel tuleb kõnealuse aine saamiseks kasutada puhast kondensaati.
Uurime, milliseid kõnealuse aine sorte saab esitada ja kuidas igat tüüpi lämmastikhapet toodetakse.
Lämmastikhappe sordid ja selle vabastamise peamised etapid
Kaasaegsetes tööstusettevõtetes toodetakse kahte tüüpi lämmastikhapet - lahjendatud ja kontsentreeritud. Lahjendatud lämmastikhappe tootmine toimub kolmes põhietapis:
- ammoniaagi muundamine (selle lõpptooteks on lämmastikoksiid);
- toodab lämmastikdioksiidi;
- lämmastikoksiidide absorptsiooni rakendamine kellveekasutus.
Kaasaegsetes tööstusettevõtetes on lahjendatud lämmastikhappe tootmine nn AK-72 skeemi alusel lai alt levinud. Kuid loomulikult on selle aine vabastamiseks ka teisi tehnoloogiaid.
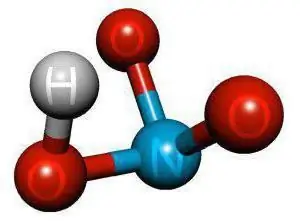
Kontsentreeritud lämmastikhappe tootmist saab omakorda teostada vastava aine taseme tõstmisega lahjendatud kujul või otsese sünteesi teel. Esimene meetod võimaldab reeglina saada happelahust kontsentratsiooniga umbes 68%, mis ei pruugi olla piisav kõnealuse aine kasutamiseks paljudes piirkondades. Seetõttu on levinud ka otsesünteesi meetod, mis võimaldab saada ainet kontsentratsioonis umbes 97-98%.
Vaatame lähem alt, kuidas ühel või teisel kujul lämmastikhapet toodetakse. Eespool märkisime, et lahjendatud ainet saab vabastada vastav alt skeemile AK-72. Uurime kõigepe alt selle eripära.
Lahjendatud happe tootmine AK-72 tehnoloogia abil
Vaatatav skeem, mille kaudu toimub lämmastikhappe tootmine, hõlmab suletud tsükli kasutamist, millega kaasneb:
- ammoniaagi muundamine;
- seotud gaaside jahutamine rõhul umbes 0,42-0,47 MPa:
- oksiidide neeldumine rõhu all suurusjärgus 1,1-1,26 MPa.
Skeemi AK-72 lõpptoode on lämmastikhape kontsentratsiooniga umbes 60%. Lämmastikhappe tootmine seesvaadeldav tehnoloogia viiakse läbi järgmiste etappide raames:
- õhu sissepääsu tagamine atmosfäärist tööstusüksusesse ja selle puhastamine;
- õhu surumine, eraldamine tehnoloogilisteks voogudeks;
- ammooniumi aurustamine, vastava gaasi puhastamine õlist ja muudest lisanditest, samuti selle järgnev kuumutamine;
- puhastatud ammoniaagi ja õhu segamine, selle segu järgnev puhastamine ja selle ülekandmine katalüsaatorile;
- lämmastikgaaside saamine ja nende jahutamine;
- kondensaadi kogumine lämmastikhappega;
- lämmastikhappe kontsentratsioon ja imendumine;
- saadud toote jahutamine ja puhastamine.
Valmis hape saadetakse hoidlasse või kliendile.
Lisaks vaadeldavale lämmastikhappe tootmise tehnoloogiale - AK-72, kasutatakse vastava aine vabastamiseks teist populaarset kontseptsiooni, mis hõlmab tööstusliku infrastruktuuri töö tagamist rõhul umbes 0,7 MPa. Mõelge selle funktsioonidele.
Toote vabastamise tehnoloogia rõhu all 0,7 MPa: nüansid
Kõnealune tehnoloogia toodab AK-72 kontseptsiooni alternatiivina kontsentreerimata lämmastikhapet. See hõlmab kõnealuse aine vabanemise järgmiste etappide rakendamist.
Esiteks, nagu ka eelmise tehnoloogia puhul, puhastatakse atmosfääriõhk. Sel eesmärgil kasutatakse reeglina kaheastmelist filtrit. Lisaks surutakse puhastatud õhk kokkuõhukompressori abil - kuni ligikaudu 0,35 MPa. Sel juhul õhku soojendatakse - kuni temperatuurini umbes 175 kraadi ja seda tuleb jahutada. Pärast selle probleemi lahendamist läheb see täiendava kokkusurumise piirkonda, kus selle rõhk tõuseb ligikaudu 0,716 MPa-ni. Saadud õhuvool kuumutatakse omakorda kõrge temperatuurini - umbes 270 kraadini lämmastikgaaside toimel. Seejärel segatakse see tööstusüksuse spetsiaalses piirkonnas ammoniaagiga. Vastav aine aktiveerub happe vabanemisel algselt gaasilises olekus, mis tekib vedeliku aurustumisel. Lisaks tuleb ammoniaak puhastada. Pärast valmistamist gaas kuumutatakse ja juhitakse segistisse samaaegselt õhuga. See segu filtreeritakse ja pärast puhastamist juhitakse ammoniaagi muundamiseks. Vastav protseduur viiakse läbi plaatina- ja roodiumisulamist võrku kasutades väga kõrgel temperatuuril - umbes 900 kraadi. Konversioonimäär on umbes 96%.
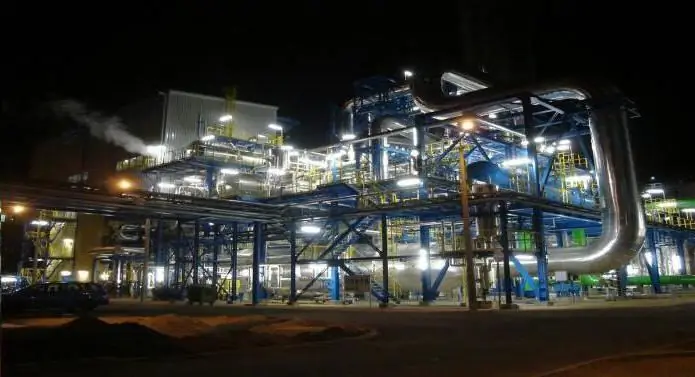
Nõrga lämmastikhappe tootmine vastav alt vaadeldavale tehnoloogiale hõlmab lämmastikgaaside moodustumist. Need tuuakse tööstusüksuse spetsiaalsesse piirkonda, kus neid jahutatakse. Tänu sellele puhastatud vesi aurustub ja kõrge rõhuga aur ilmub. Tööstusüksuse vastava ala kaudu liiguvad lämmastikgaasid oksüdeerijasse. Tuleb märkida, et nende oksüdatsioon toimub osaliselt juba eelmiselhappe tootmise etapid. Kuid oksüdeerijas muutub see veelgi intensiivsemaks. Sel juhul kuumutatakse lämmastikgaase temperatuurini umbes 335 kraadi. Seejärel jahutatakse need spetsiaalses soojusvahetis ja saadetakse seejärel kondensaatorisse.
Pärast seda moodustub nõrga kontsentratsiooniga lämmastikhape. Sellest on vaja ülejäänud dilämmastikgaasid eraldada - selleks kasutatakse separaatorit. Sellest juhitakse lämmastikhape tööstusüksuse neeldumisalasse. Seejärel voolab hape alloleva seadme piirkondadesse. Samal ajal interakteerub see lämmastikoksiididega, mille tagajärjel selle kontsentratsioon suureneb. Väljundis on see umbes 55-58%. Tavaliselt sisaldab see lahustunud oksiide, mis tuleb eemaldada: selleks saadetakse aine seadme puhastusalasse. Kuumutatud õhu abil eraldatakse happest oksiidid. Valmistoode pannakse lattu või saadetakse kliendile.
Kontsentreeritud happe tootmine: otsene süntees
Võttes arvesse, kuidas toimub lahjendatud lämmastikhappe tootmine, uurime kontsentreeritud aine vabanemise iseärasusi. Happe tootmine otsese sünteesi teel toorainest lämmastikoksiidide kujul on üks kõige kuluefektiivsemaid tehnoloogiaid, mida vastava profiiliga ettevõtetes kasutatakse.
Selle meetodi olemus seisneb keemilise reaktsiooni stimuleerimises kindlaksmääratud aine, vee ja hapniku vahel rõhu all umbes 5 MPa. Tehnoloogia, mille abil lämmastikhapet toodetaksekontsentreeritud tüüp lahjendatud baasil, omab nüanssi: lämmastikdioksiidi vedelaks muutumise tagamine on võimalik atmosfäärilähedasel rõhul ja temperatuuril. Mõne reaktsiooni korral ei ole vastava aine kontsentratsioon siiski piisav, et see normaalsel rõhul vedelasse olekusse viia, ja seda tuleb suurendada.
Kontsentreeritud happe tootmine lahjendatud happe põhjal
Sel juhul eeldatakse, et hape on kontsentreeritud absorbeerivate ainete abil - nagu väävel, fosforhape, erinevad nitraatide lahused. Lahjendatud väävelhappel põhineva kontsentreeritud lämmastikhappe tootmise peamised etapid on järgmised.
Esiteks jagatakse tooraine kaheks vooluks: esimene juhitakse aurustisse, teine - tööstusüksuse külma piirkonda. Väävelhape juhitakse seadme piirkonda, mis asub teise lahjendatud lämmastikhappe voolu kohal. Seadme alumisse ossa suunatakse omakorda aur, mis soojendab kasutatavat segu, mille tulemusena aurustub sellest lämmastikhape. Tema aurud tõusevad seadmest üles, misjärel need eemaldatakse külmkappi. Seal kondenseeruvad happeaurud - kuni selle kontsentratsioon jõuab 98-99%.
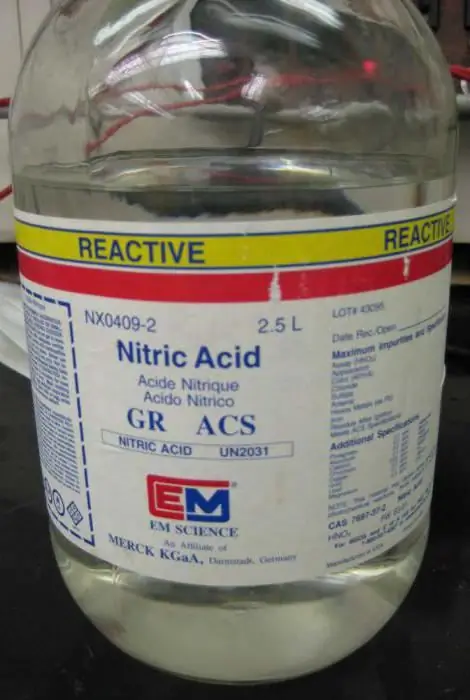
Samal ajal neeldub hape osa selles tootmisetapis olevatest lämmastikoksiididest. Need tuleb tootest eraldada: enamasti kasutatakse selleks lämmastikhappe aurud, mis suunatakse kondensaatorisse. Ekstraheeritud lämmastikoksiidid, aga ka happeaurud, mis ei moodustanud kondensaati, suunatakse aparaadi teise piirkonda - absorptsiooniks, kus neid töödeldakse veega. Selle tulemusena moodustub lahjendatud hape, mis juhitakse uuesti kondenseerumisele ja jahutamisele. Valmistoode saadetakse lattu või kliendile.
Väävelhappega kontsentreerimise omadused
Peamine ülesanne, mis iseloomustab lämmastikhappe tootmist tööstuses, on selle kulutõhusa ja tõhusa kontsentreerimise rakendamine. Selle lahendamiseks optimaalse skeemi väljatöötamiseks on mitu lähenemisviisi. Kasulik on kaaluda neid, mis on ühed levinumad.
Eespool märkisime, et väävelhapet saab kasutada kõnealuse aine kontsentreerimiseks. Selle kasutamise tõhususe suurendamiseks on üsna levinud viis - lämmastikhappe kontsentratsiooni esialgne suurendamine aurustamise teel. Optimaalselt on vastava aine kontsentratsioon enne väävelhappega töötlemist umbes 59-60%. Tuleb märkida, et praktikas iseloomustab seda lämmastikhappe tootmise tehnoloogiat madal keskkonnasõbralikkuse tase. Seetõttu on väävelhappe kasutamisele alternatiivina levinud nitraatide kasutamine. Uurime nende eripärasid üksikasjalikum alt.
Nitraatidega kontsentratsioon
Kõige sagedamini kasutatakse vaadeldava probleemi lahendamiseks magneesium- või tsinknitraate, mis iseloomustab lämmastikhappe tootmist ammoniaagist. Esiteks on see meetodist oluliselt keskkonnasõbralikummis hõlmab väävelhappe kasutamist. Lisaks tagab see tehnoloogia lämmastikhappe kõrgeima kvaliteedi lõpptootena.
Samas on sellel mitmeid puudusi, mis määravad raskuste ilmnemise selle laialdasel kasutamisel. Esiteks on see tootmisprotsessi üsna kõrge hind. Lisaks hõlmab see tehnoloogia paljudel juhtudel tahkete jäätmete tootmist, mille töötlemine võib olla keeruline.
Katalüsaatorite kasutamine lämmastikhappe tootmisel
Kasulik on kaaluda, milliseid muid aineid kasutatakse koos peamiste toorainetega kõnealuse toote tootmiseks lämmastikhappe tööstuslikul (enamasti peetakse selleks katalüsaatoreid) tootmisel. Kõnealuste ainete kasutamine on tingitud vajadusest suurendada happetootmise kasumlikkust, suurendada selle toodangu dünaamikat tööstusüksuses.
Katalüsaatori põhinõue kõnealuse toote valmistamisel on toime selektiivsus. See tähendab, et see peab mõjutama peamist keemilist reaktsiooni, mõjutamata kõrvalprotsesse. Kõige sagedamini kasutatakse happe tootmisel katalüsaatoreid, mis sisaldavad plaatinat.
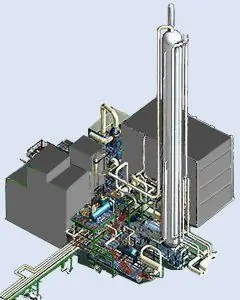
Eespool märkisime, et kui nõrg alt kontsentreeritud aine vabaneb kõrgendatud rõhul, kasutatakse plaatina ja roodiumi baasil katalüsaatoreid. Mõnel juhul kasutatakse ka pallaadiumilisandiga sulameid. Kuid peamine metall neis onplaatina, selle sisaldus on tavaliselt vähem alt 81%. Katalüsaatori olemus on sel juhul stimuleerida peamise keemilise reaktsiooni kiiret läbimist. Reeglina läbib see välise difusiooni sektsiooni.
Protsess sõltub hapniku difusiooni piiridest katalüsaatori pinna suhtes. See omadus põhjustab ammoniaagi, lämmastikhappe tootmise peamise tooraine, suurema kontsentratsiooni ühe või mõnikord katalüsaatori pinnal, võrreldes kontsentratsiooniga õhus. Võimalik on suurendada erinevate kõrvalreaktsioonide erikaalu, mille puhul täheldatakse mittetäielikku oksüdeerumist ja lämmastiku või selle oksiidi moodustumist. Sellega seoses peab pinna lähedal hapnikku olema piisavas koguses ammoniaagi väljatõrjumiseks. Sel juhul on võimalik saavutada piisav alt sügav oksüdatsioon.
Võib märkida, et koos plaatina katalüsaatoritega osalevad lämmastikhappe tootmises ka kombineeritud ained. Eelkõige raud-kroom. Need võivad oluliselt vähendada kõnealuse aine tootmist iseloomustavaid majanduskulusid.
Niisiis oleme kaalunud lämmastikhappe tootmismeetodeid, tuvastanud selle peamised tüübid. Kui palju lämmastikhappe tootmise etappe on vaja rakendada, sõltub selle tüübist, samuti vastava aine vabastamise spetsiifilisest tehnoloogiast. Nüüd oleks kasulik mõelda, millised raskused iseloomustavad selle paljudes majandusvaldkondades nõutud toote tööstuslikku tootmist.
Peamised probleemidlämmastikhappe tootmine
Niisiis, nagu me juba teame, hõlmab lämmastikhappe tootmine kontaktmeetodil - tänapäevases tööstuses üks levinumaid - katalüsaatori kasutamist, et kiirendada ammoniaagi oksüdeerumist ja suurendada ammoniaagi saagist. toode. Peamiseks probleemiks vaadeldava toote valmistamisel on vastava katalüsaatori üsna kõrge hind. Selle selektiivsus ei saavuta aga alati optimaalset väärtust. Lisaks võib tootmise käigus kaduda märkimisväärne osa plaatinast, mida kasutatakse katalüsaatori põhielemendina. Selle tulemusena jällegi väheneb toote toodangu kuluefektiivsus.
Teine probleem, mis iseloomustab lämmastikhappe tootmist, on keskkond. Eespool märkisime, et väävelhapet saab kasutada tooraine kontsentratsiooniga ning vastava tootmistsükli läbimisel tekivad kahjulikud ained. Alternatiiviks võib sel juhul olla nitraatide kasutamine, kuid see tähendab jällegi majanduskulude suurenemist. Tänapäevaste tootjate jaoks on keskkonnategur aga sama oluline kui tootmise kasumlikkuse tase.
Soovitan:
Mootoriõli tootmine: omadused, tehnoloogia ja tootmisprotsess
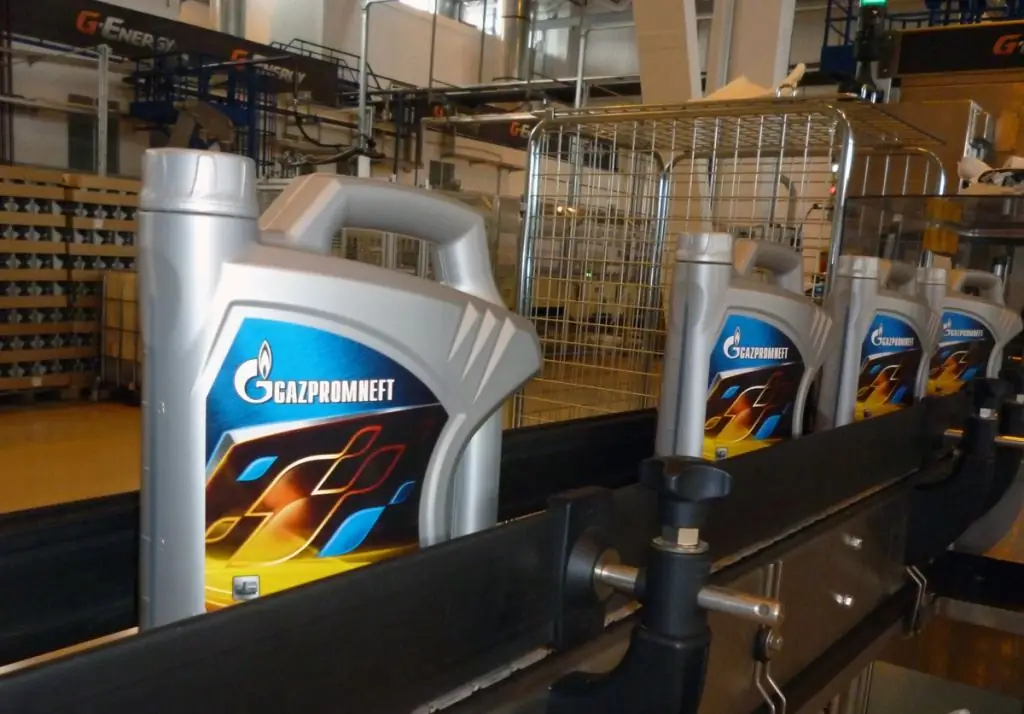
Mootoriõli, nagu iga teisegi õli tootmine ei ole täielik ilma tooraineta – aineta, millest lõpptoode saadakse. Mineraalõli on valmistatud naftast. Kuid enne määrdeainete tehasesse jõudmist peab see läbima mitmeid puhastusi naftatöötlemistehastes
Vineeri tootmine: tehnoloogia, protsessi peamised etapid ja materjali kasutusvaldkonnad
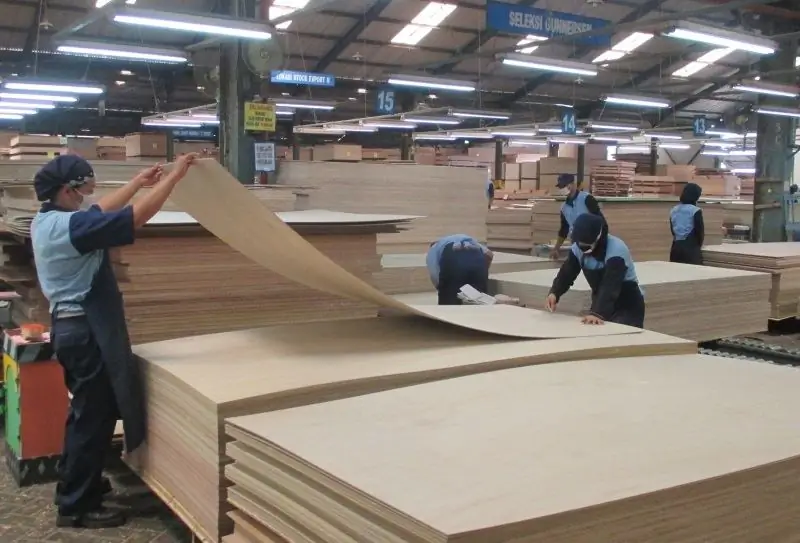
Vineer on üks odavamaid ja praktilisemaid ehitusmaterjale. Vaatamata mitmekihilisele struktuurile on seda lihtne paigaldada ja seda saab kodus ilma eriseadmeteta töödelda. Vineeri standardtootmine hõlmab puitlamellide kasutamist, mille õigel töötlemisel saate mitmesugustele ohtudele vastupidava viimistlusmaterjali
Polüpropüleen – mis see on? Definitsioon, materjali tehnilised omadused, rakendus tööstuses ja igapäevaelus
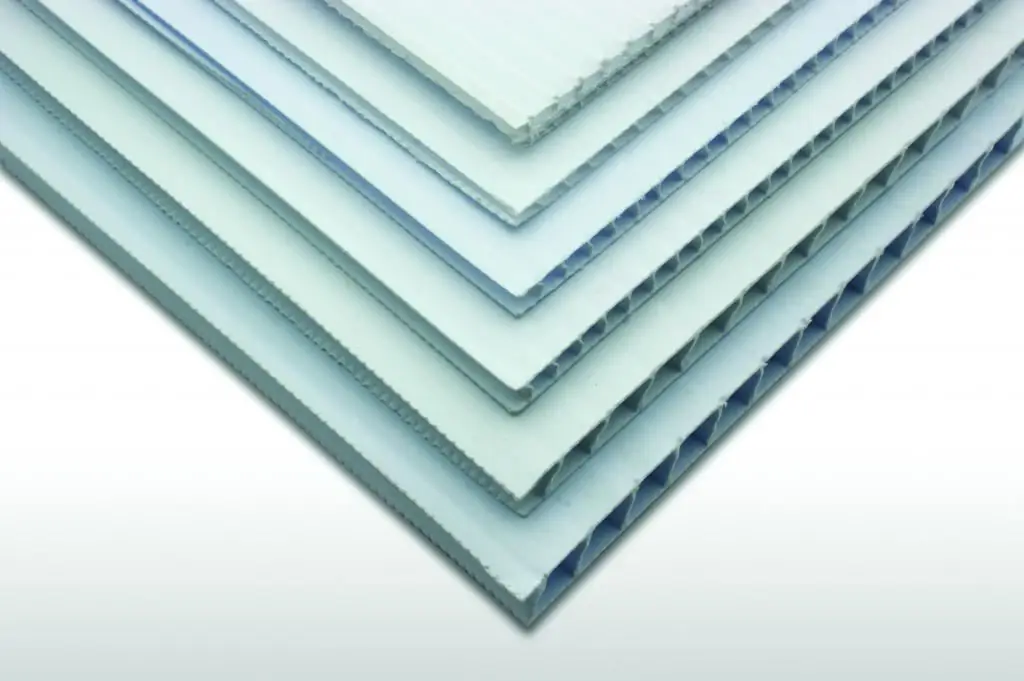
Polüpropüleenist saate oma kätega küttesüsteemi ehitada. Materjal on taskukohane ja kerge. Enne töö alustamist on vaja määrata ühenduspunktid ja mõista paigaldusmeetodit. Torude jootmiseks tuleb tooted mõõtu lõigata. Vuugid peavad olema ühtlased ja täisnurga all. Sektsioonid rasvatustatakse, pärast lõikamist eemaldatakse pinn alt laastud
Madalrõhukütteseadmed: määratlus, tööpõhimõte, tehnilised omadused, klassifikatsioon, disain, tööomadused, rakendus tööstuses
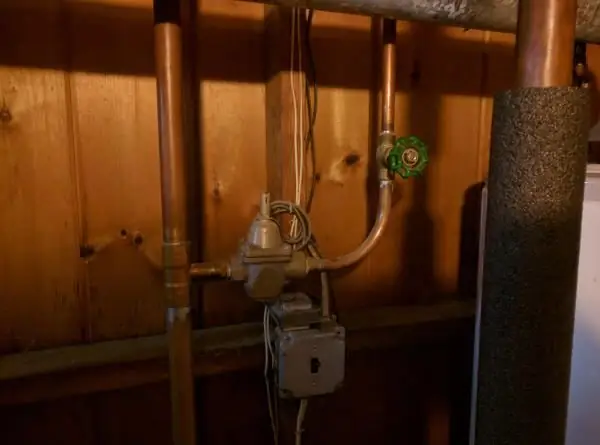
Madala rõhuga kütteseadmeid (LPH) kasutatakse praegu üsna aktiivselt. Erinevates koostetehastes toodetakse kahte peamist tüüpi. Loomulikult erinevad need ka oma tööomaduste poolest
Mineraalvee tootmine: tehnoloogia, etapid, seadmed
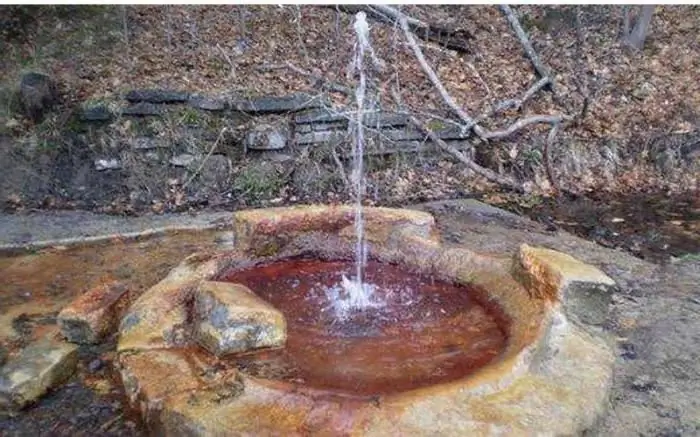
Paljudele tundub mineraalvee tootmine väga lihtne. Ja esmapilgul võib see nii tunduda. Lõppude lõpuks hoolitses loodus ise toote kvaliteedi ja eeliste eest. Ja ettevõtjal tuleb vaid kaev puurida ja kraan kinni panna, et vesi kohe pudelitesse voolaks. See on vaid pinnapealne teadmine asjast