2025 Autor: Howard Calhoun | [email protected]. Viimati modifitseeritud: 2025-06-01 07:13
Erinevaid rööpa defekte on üsna palju. Kõik need tekivad erinevatel põhjustel. Kokku on neli peamist puudulikkuse tüüpi, mille tõttu tekib rike. Kehv rööbastee tootmis- ja keevitustehnoloogia on esimene kulumise põhjus. Teine põhjus on see, et tee sisu on liiga madal. Materjalil on selline parameeter nagu kontakti väsimustugevus ja kui see parameeter ei ole piisav alt kõrge, siis muutuvad ka rööpad kasutuskõlbmatuks. Nende rajatiste rikke viimane põhjus on nende kohal liikuva veeremi mõju.
Rikke põhjused
Kasutamise ajal arvutatakse rööbaste defektid ja nende tõenäoline esinemine mitme fakti põhjal. Esiteks on oluline tegur tonnaaž, mis on marsruudi lõigul läbinud. Teiseks mängib rolli veeremi telje koormus. Rongide seisukorda võib mõjutada ka rongide kiirus. Praktika ja vaatlus näitavad sedasoojal aastaajal, see tähendab kevadel ja suvel, katkiste radade arv väheneb. Sügisel see näitaja veidi suureneb ja talvel 2-3 korda võrreldes sooja aastaajaga. Sellel on seletus ja see seisneb selles, et madalatel temperatuuridel iseloomustab metalli suurenenud rabedus. Teisisõnu, selle löögitugevus on viidud miinimumini. Suurim protsent rööbaste defektidest tingitud rööbastee rikkeid esineb märtsis, kui räägime riigi Euroopa osast, ja ka aprillis, kui see puudutab ida- ja Siberi piirkondi.
Selliste probleemide tuvastamiseks kasutatakse veadetektoreid. 96,5% kõigist tuvastatud probleemidest saab tuvastada eemaldatavate või kaasaskantavate seadmete abil. Veel 2% tuvastatakse auto veadetektorite abil ja veel 1% selle seadme muude mudelite abil. Väga oluline on märkida, et on olemas rööbaste defektide klassifikatsioon ja nende kirjeldus numbrite abil. Seda tehti selleks, et oleks võimalik teostada rööbaste staatilist arvestust.
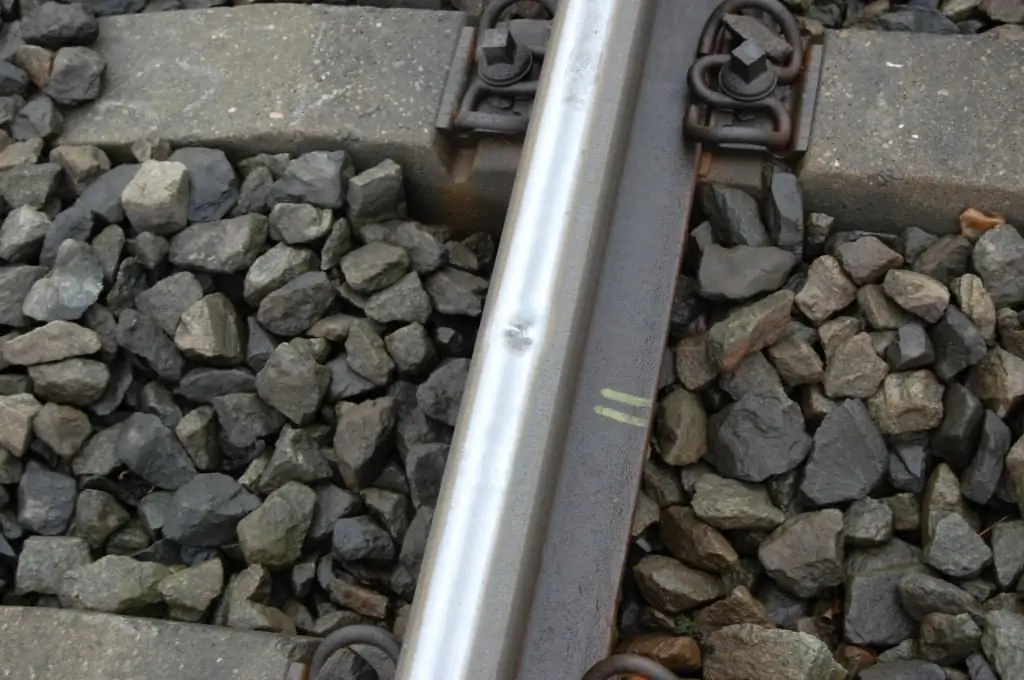
Klassifikatsioon
Kõik kahjustused, purunemised või defektid rajalõikudel on tähistatud ühtse numbrisüsteemi abil. Kaks esimest numbrit on peamised ja kolmas on abinumbrid. Esimene number näitab rööpa defekti või kahjustuse tüüpi. Lisaks näitab see ära ka probleemi asukoha raudteelõigul. Teine number kirjeldab defekti tüüpi või kahjustust, võttes arvesse selle põhjustilmunud. Kolmas abinumber näitab defekti või kahjustuse asukohta rööpa pikkuses. Täpsem alt kirjeldatakse rööbaste defekte ja nende klassifikatsiooni esimese märgi numbritega 1 kuni 9.
- Kui esimene number on 1, siis see tähendab, et rööpapea veerepinnal tekkis metalli lõhenemine ja koorumine.
- Kui arv on 2, tähendab see, et rööbastee lõigul leiti rööpapeas põikipraod.
- Arv 3 näitab ka rööpapeas esinevaid, kuid pikisuunalisi pragusid.
- Arv 4 näitab, et on toimunud plastilised muutused, st muljumine, vertikaalne, külgmine või ebaühtlane pea kulumine.
- 5 on rööpa kahjustused ja defektid, mis mõjutavad kaela.
- 6 on rööbaste talla rike või kahjustus.
- 7 - see on üsna tugev deformatsioon, kuna see arv näitab kõverate esinemist kogu raudteelõigul.
- Kui vertikaal- ja horisonta altasapinnas tekivad katkestused, määratakse esimese asemel number 8.
- Kõik muud rööpa defektid, kahjustused jms, mis ei kuulu ühtegi ül altoodud kategooriasse, on tähistatud numbriga 9.
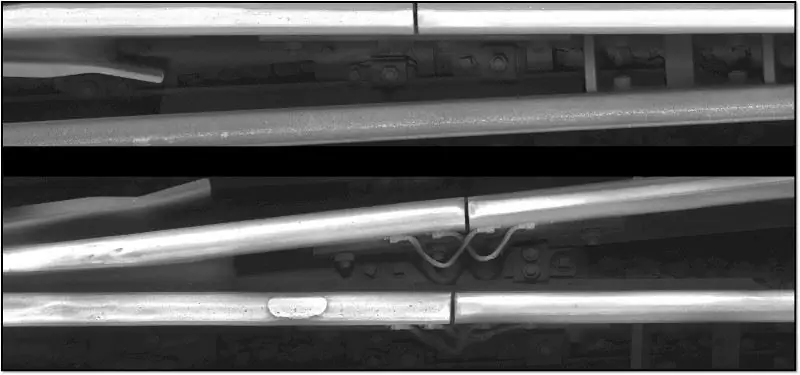
Numbrite tähenduse määramine
Rööpa veakoodi põhinumbritest teisel on samuti palju väärtusi, täpsem alt 0 kuni 9.
- Kui teine number on 0, tähendab see, et defekt tekkis sellest, et selle raudteelõigu loomisel esines kõrvalekaldeid tehnoloogiasttootmine.
- Arv 1 näitab, et rööbaste tootmiseks kasutatud terase metallurgiline kvaliteet oli ebapiisav. Samuti on võimalik, et terase tugevus oli väiksem kui normaalseks tööks vajalik.
- 2 - näitab, et otste töötlemisel tehti vigu, mille tõttu teelõik ebaõnnestus. Lisaks sisaldab see ka mõningaid puudusi, mis ilmnevad rööpaprofiilide töötlemisel.
- 3 - need on raudtee rööbaste defektid, mis tekkisid objekti jooksva hoolduse juhendi nõuete rikkumise tõttu. Siia kuuluvad ka kahjud, mis on põhjustatud asjaolust, et rikuti sulatusahju poldiavade töötlemise tehnoloogia põhimõtteid.
- Kui teine number on 4, siis see tähendab, et probleemid rööbastega tekkisid veeremi spetsiifilise mõju tõttu neile, näiteks libisemise tõttu. See hõlmab ka kahjusid, mis tulenevad asjaolust, et veerem ei läbi nõuetekohast kontrolli või sõidurežiime rikutakse.
- Arv 5 hõlmab kõiki kahjustusi, mis on põhjustatud mis tahes mehaanilisest väljastpoolt tulevast mõjust, näiteks tööriistaga löömine, rööpa löömine vastu siini jne.
- Üsna levinud ühise siini keevitusdefektid on põhjustatud ebakorrapärasusest keevitusmasina töös. Need esinevad keevisliidetes ja on nummerdatud 6.
- 7 - probleemid, mis on seotud rööbaste tööga liigendites.
- 8 - need on vead, mis tekivad rööbaste pinnakatte tõttu, samutirööbaste ühenduste ebaõige keevitamise tõttu.
- Kõik korrosioonist põhjustatud probleemid on nummerdatud 9.
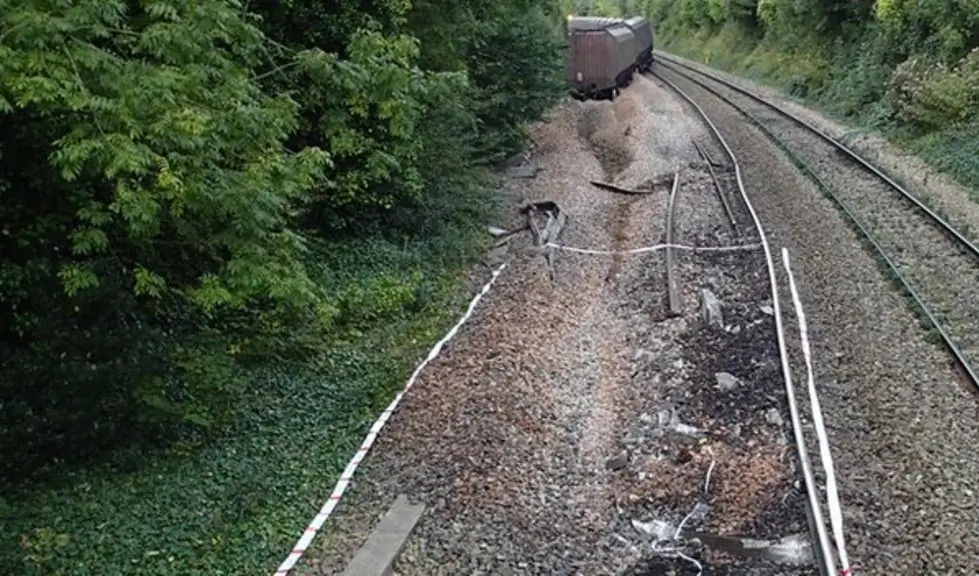
Väärib märkimist, et rööbaste purunemisest tingitud rööbaste lõigu rike on mitme põhjuse samaaegse mõju tagajärg. Kõige sagedamini selgub, et raudtee puudulik hooldus kiirendab oluliselt nende vigade teket, mis tekkisid konstruktsiooni kokkupanemisel või keevitamisel. Seetõttu on põhjuse kindlaksmääramine keeruline, kuna on vaja täpselt leida rikke peamine allikas. Raudtee rööbaste defektid või õigemini nende numeratsioon on ka kolmanda kohaga.
- 0 näitab, et probleem esineb kogu rööpa pikkuses.
- 1 tähendab, et probleem on liigeses, mitmes kohas. Võib-olla on katki poltliide, mis asub siini otsast vähem alt 750 mm kaugusel. Kui me räägime keevisliitest, siis 200 mm kaugusel sümmeetriliselt 100 mm mõlemal pool keevisõmbluse telge.
- 2 näitab, et probleemid on kusagil väljaspool liigest. Kui me räägime poltühendusest, siis tuleb vaadelda 440 mm kaugust sümmeetriliselt 220 mm mõlemal pool rööpa jaluse keevisõmbluse telge.
Rööpa keevitamise defektid ja muud kahjustused jagunevad samuti nelja kategooriasse, olenev alt nende arenguastmest. Seal on DP, D1, D2 ja D3 aste. Kõige ohtlikumad on DP. See tähistus näitab, et kahjustus on saavutanud kriitilised väärtused või suurused. Sellised alad peaksidkõigepe alt asendada. D1- ja D2-kategooria defektid parandatakse vastav alt kehtestatud korrale, mis arvestab probleemi intensiivsust. D3-kategooria defektidega rööpad vahetatakse välja ainult siis, kui raja distantsi pea nii otsustab. Otsus tehakse töödejuhataja poolt pärast plaanilist ülevaatust edastatud andmete alusel ning arvestades defekti arenguastet. Selle tulemusel selgub, et rööbaste defektide koodid koosnevad kolmest numbrist, samuti märgitakse nende arenemisaste lõigul.
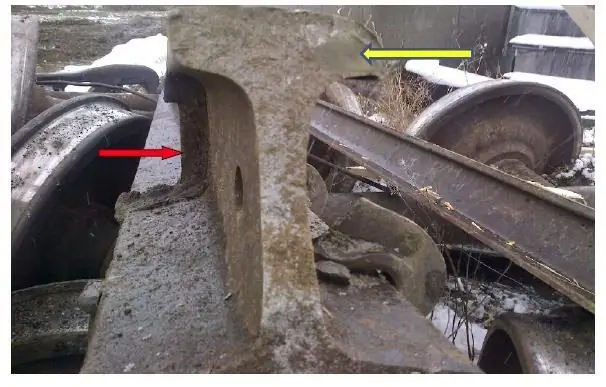
Vigade tuvastamine
Vigade tuvastamine on protseduur raudtee struktuuris esinevate puuduste tuvastamiseks spetsiaalsete veatuvastusseadmete abil. Väärib märkimist, et rööpad läbivad selle protseduuri mitu korda. Esimene vigade avastamine toimub rööbaste v altsimistehases, kui on vaja hinnata valmis töö kvaliteeti. Järgmine taatlusprotsess toimub juba töötingimustes ehk teel. Lisaks toimub taatlus rööbaste keevitamise töökodades, kus keevitatakse mitte ainult uusi, vaid ka remonditakse või keevitatakse vanu konstruktsioone.
Vigade tuvastamise protseduur on mõeldud eelkõige nende ohtlike rööbaste defektide tuvastamiseks, mis on konstruktsiooni sees, st neil ei ole veel välisküljel vigu. See võimaldab kahjustatud konstruktsiooni õigeaegselt asendada.
Probleemide tüübid
Praegu kõikvõimalikud vead, nende kõrvaldamise viisid, esinemise põhjused,nende määramise vahendid jne on esitatud "Regulatiiv- ja tehniline dokumentatsioon NTD / TsP 2002". Lisaks väärib märkimist, et on olemas ka eksperimentaalne dokumentatsioon, samuti rööbaste defektide klassifikatsioon NTD / TsP 1-93, mille järgi jagunevad kõik probleemsed raudteelõigud äged alt defektseteks (OD) ja defektseteks (D).). See on NTD / CPU 2002 abiga defektide D kategooria, mis jaguneb sõltuv alt esinemise põhjusest, leviku astmest ja asukohast marsruudil suureks arvuks tüüpideks.
Jõvasti defektsed rööpad on need, mis kujutavad otsest ohtu rongi liikumisele, kuna vea mõjul võivad need kokku kukkuda otse rongi rataste alla või põhjustada veeremi lahkumise rada. Kui selline lõik leitakse, tuleb see kohe vahetada kas uue vastu või kilomeetri laost vana vastu. Kui raudteerööbastel avastati uued defektid enne nende kasutusgarantii lõppemist või kui nendest lasti läbi dokumentatsioonis märgitust väiksem tonnaaž, esitatakse pretensioon metallurgiatehase peale, kus need valmistati. Kui viga avastati keevisühendusel ka enne tähtaega, siis esitatakse kaebus rööpakeevitustehasele.
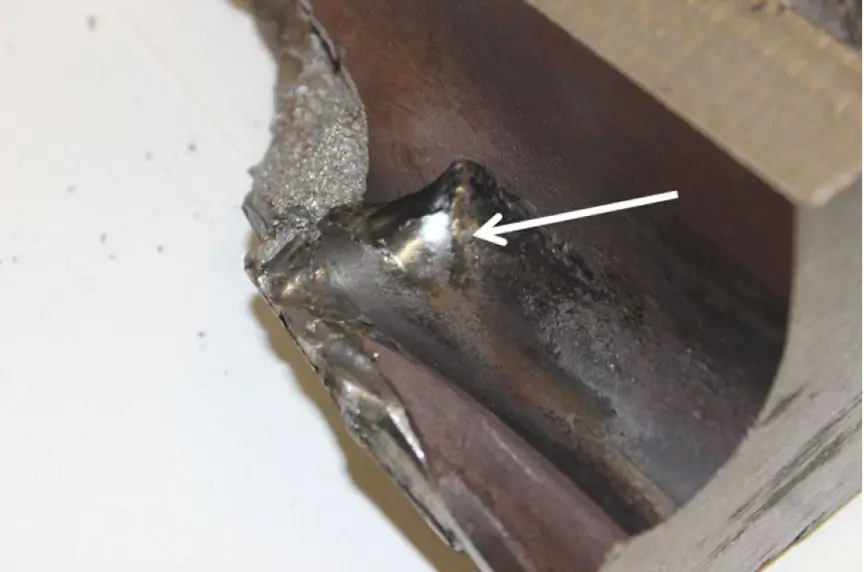
Defektsete rööbaste hulka kuuluvad need rööbastee lõigud, mis pika kasutusea tõttu hakkasid kasutuskõlbmatuks muutuma. Sellistes piirkondades on oodata puuduste teket. Siiski peavad nad siiski tagama veeremi ohutu läbipääsu. Kuigi sisseMõnel juhul kehtestatakse sellise rajalõigu läbimisel kiiruspiirang. Rööbaste defektide uus väljaanne ja nende klassifikatsioon on täpselt ära toodud normatiiv- ja tehnilises dokumendis NTD / CPU 2002. Võimalike probleemide koodiväärtused on toodud ülal.
Jagamine terav alt defektseteks ja defektseteks piirkondadeks
Dokumentatsioon näitab kiirust, millega rongil on lubatud liikuda mööda konkreetset rööbastee lõiku. Kui defekti arenguaste kuulub DP rühma, siis liikumiskiirus kuni kõrvaldamise hetkeni ei ületa 40 km/h. Kategooria D1 lubab kiirust mitte rohkem kui 70 km / h, D2 - mitte rohkem kui 100 km / h. D3 rühma kuuluvad vead ei sea piirangut veeremi liikumiskiirusele.
Lisaks on iga defektsete rööbaste rühma asendamiseks määratud ajakava. Kui kehtestatud perioodi jooksul asendust ei toimu, asendatakse kategooria kõrgema kategooriaga. Teisisõnu, DP3 läheb D2-sse, D2 D1-sse, D1 DP-sse. Loomulikult karmistuvad iga üleminekuga asendustähtajad ning vastav alt kehtestatud normidele suureneb ka liikumiskiirus.
Rööbaste defektid ja nende uus klassifikatsioon vastav alt NTD/CPU-le määratlevad ka probleemid, mis muudavad rööbastee lõigu äged alt defektsete või lihts alt defektsete rööbaste olekusse. OD-le kuuluvad sellised probleemid nagu:
- Rööbaste peas olevate põiki-, piki- või külgsuunaliste pragude tekkimine. Kõige sagedamini kuuluvad jaotused teise ja kolmandasse rühma ning nende koodid on 20, 21, 24, 25.
- Mõranemine poldiavades kooskood 53, samuti praod rööpa kaelas, olenemata suurusest, samuti koodidega 50, 55, 59 ja 56.1.
- Koodiga 69 rööbaste korrosiooni või lokaalse kulumise tekkimine korrosiooniväsimisest tekkinud pragude, koodidega 60, 64, 65, 66 siinide talla väljalõhkumine, samuti rööbaste põikmurrud.
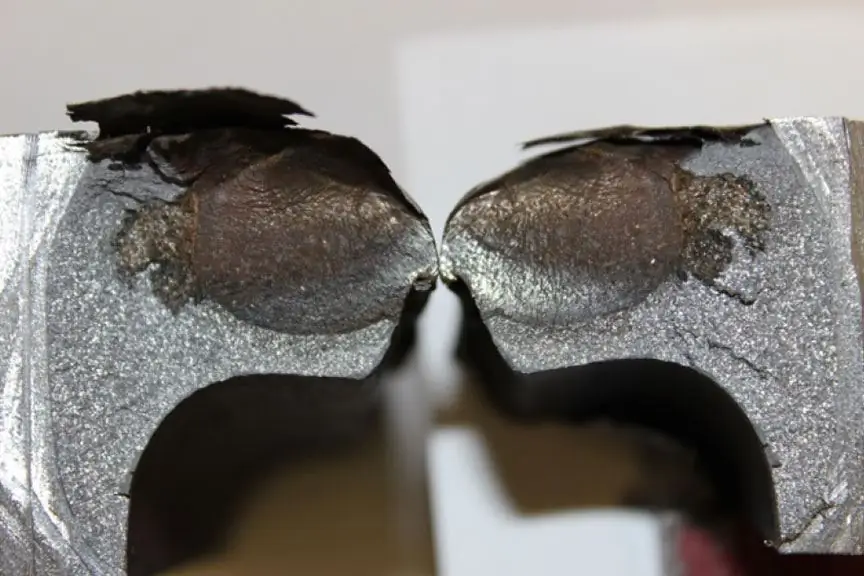
Nende uute defektide ilmnemine viib selleni, et isegi uus raudteelõik läheb ML-i ja see tuleb kiiresti välja vahetada. Defektsed rööpad tuvastatakse vastuvõtu- ja väljumisradadel mitme märgi järgi. Nende hulka kuuluvad:
- normaliseeritud vähendatud koodi 41+44, küljekoodi 44 või rööpapea vertikaalse kulumise ületamine;
- metalli hakkimine, kui sügavus ei ületa 3 mm ja pikkus on 25 mm;
- veeremi rataste libisemine, lainetav kulumine.
Samuti tasub lisada, et suurim protsent normaalrööbaste üleminekust defektikategooriasse toimub seetõttu, et materjalil puudub kontaktväsimustugevus. Sellised rööbaste ja pöörmeelementide defektide probleemid, mida ka rööbastele paigaldatakse, on klassifitseeritud koodidega 11 ja 21. Samuti on üsna sageli põhjuseks probleem 44, mis tähendab rööpapea tugevat külgmist kulumist. Üsna sageli esineb siini talla korrosiooni - 69.
Eriti ohtlikud defektid ja põhjused
Esiteks tuleb rööbaste kontrollimisel pöörata tähelepanu nendele riketele, mis on põhjustatudmetalli "väsimus". Neid peetakse kõige ohtlikumaks. Täpsem alt näeb see välja selline. Rongi ratas puutub liikumise ajal rööpaga kokku üsna väikesel alal. Just selle väikese ala kaudu edastatakse liikuva rongi tekitatav tohutu pinge. Just need kontaktpinged, eriti kui need tekivad rööpapea vahetus läheduses, põhjustavad selle lõhenemist või metalli lõhenemist. Mida rohkem rattaid seda piirkonda läbib, seda rohkem metall "väsib". Just seetõttu on defektid 11.1-2 põhjustatud sellisest probleemist nagu materjali madal kontakttugevus. Selle probleemi vältimiseks või vähem alt selleks, et rööpad taluksid rohkem liikumisi, on vaja suurendada tooraine tugevust.
Metalli kihistumise või lõhenemise põhjuseks võivad olla ka juuksepiirid, päikeseloojangud või vangistus, mis võivad v altsimise ajal rööbaste pinnale ilmuda.
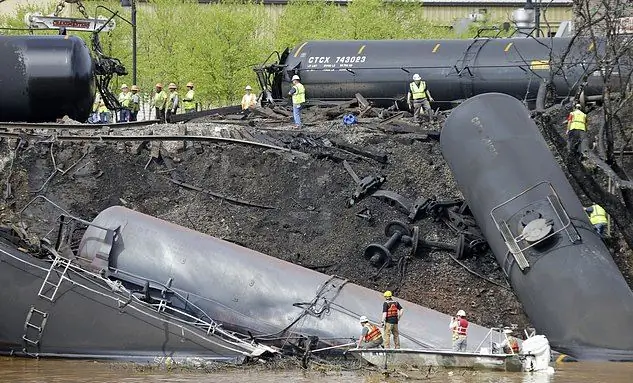
Selliseid rööbaste defektide rühmi nagu 20.1-2 ja 21.1-2 peetakse väga ohtlikeks. Mis puudutab teist vigade rühma, siis üsna sageli ilmnevad need pea sisemiste pragude või väliste pragude kujul, mis tekivad peas oleva filee piirkonnas. Kui selline probleem ilmneb, võib rööbas hiljem liikuva rongi raskuse all paljudeks väikesteks tükkideks puruneda. Loomulikult toob see kaasa õnnetuse ja suure tõenäosusega läheb rong rööbastelt välja. Mis puudutab probleeme koodiga 20.1-2, siis needtekivad peas endas ja nende väljanägemise peamine põhjus on puudujäägid tootmistehnoloogias.
Raudtee defektid halva ülevaatuse tõttu
Väärib märkimist, et 23. oktoobril 2014 kinnitati rööbaste defektide klassifikatsioon 2499 NTD / CPU. See dokument jõustus 1. septembril 2015 ja dokument ise sisaldab 140 lehekülge. Lisaks võeti vastu ka uus radade korrashoiu juhend 2288. See dokument jõustus 03.01.2017.
Sellised vead nagu 11,1-2 ja 21,1-2 on üsna sageli tingitud ka sellest, et teemeistrid jälgivad halvasti rööbaste seisukorda. Kui esimesel tööperioodil ilmneb vale rööpa alamkalle, nihkub põhipinge sektsiooni keskpunktist servale, kus asub pea, mis loomulikult toob kaasa selle kiire kulumise. Defektide esinemissagedus suureneb oluliselt ka rööpa keermete sileduse rikkumise korral. Lisaks on oluline märkida, et nende probleemide ilmnemise protsess on tugev alt seotud mitte ainult rööbasteede ebaõige hooldusega, vaid ka rongi enda veereva osa hooldamise rikkumistega. Kui auto ratastele ilmuvad mõrad, liugurid ja muud vead, mõjutab see oluliselt metalli väsimustugevust ja selle arengut.
Lisaks peale tekivad probleemid sageli ka rööbaste kaelas - põhiprobleemiks on praod poldiaukude piirkonnas. Kõige sagedamini tekib pragu poltühenduse kontuurist ja lahkub seejärel 45-kraadise kaldega horisondi suhtes. Tõhus vahend selliste pragude vastu võitlemisekson liigeste kvaliteetne sisu. Ehk siis on vaja poldid võimalikult tugevasti kinni keerata, et vältida rööbaste vajumist või vajumist. Kaelalõhed tekivad sageli ka kohtadesse, kus siini pea läheb talla sisse. Sellise defekti ilmnemise peamine põhjus on valesti valitud rööpa alamkalle.
Mis puutub tallasse, siis siin pole enamasti mitte ainult pragusid, vaid ka torke, juuksepiire. Kõik see toob kaasa raudtee rööbaste purunemise, pikisuunaliste pragude ilmnemise ja kiirendab korrosiooniprotsessi. Parim viis paljude talladefektide lahendamiseks on paigaldada elastne padi, mis asetatakse otse siinitalla alla.
Defektide asukoht ja nende nimetused
Praegu on üsna suured tabelid, mis näitavad ära peamised rööpa defektid, mis võivad tekkida. Samuti näitavad need koha, kus see või teine kahjustus tekib, probleemi kood on täpselt märgitud. Sellised tabelid näevad välja sellised.
Probleemi kirjeldus | Kahjustuse asukoht rööbastel | Defektikood |
Rööbaste tootmistehnoloogia rikkumise tõttu võivad pea v altspinnal tekkida sellised probleemid nagu praod või metalli lõhenemine | Liigendist sisse ja välja | Sõltuv alt asukohast võib kood olla vastav alt 10.1 või 10.2 |
Mõrad või mõrad võivad tekkida ka pea küljel võifilee peal. Need tekivad seestpoolt suure hulga mittemetalliliste kogumite mõjul | Liigendist sisse ja välja | Nagu ka eelmisel juhul, võib kood olenev alt kahjustuse asukohast olla 11.1 või 11.2 |
Turvise pinnale võib tekkida metallilõhe. Põhjus on selles, et poltide ühenduskohtades suureneb dünaamiline efekt | Ristmikul | see kahjukood on 13.1 |
Pärast garantii alla antud tonnaaži lõppemist võib pea turvise pinnal keevisliite piirkonnas esineda metalli lõhenemist | Rööpa keevisõmbluste defekt | Veakoodid 16.3 ja 16.4 |
Sarnane lõhenemisprobleem, kuid enne, kui garanteeritud tonnaaž on üle rööbaste aetud | Keevisliide | Defekt 17.3 ja 17.4 |
Võimalik, et libisemisest või libisemisest tulenevate termomehaaniliste mõjude mõjul võivad peas tekkida põikipraod, näiteks | Esineb nii õmbluse sees kui väljas | 24,1 ja 24,2 |
Keevitustehnoloogia või keevisõmbluste töötlemise rikkumise tõttu võivad peas tekkida põikipraod. Oluline on lisada, et see võib viia rööbastee rikkeni kohe pärast garantiitonnaaži täitmata jätmist | Keevisliide | 26,3 ja 26,4 |
Kui ilmneb sama probleem, mis eelmisel juhul, kuid enne selle vahelejätmistgaranteeritud tonnaaž, siis kantakse probleem üle teise kategooriasse | Keevisliide jääb asukohaks | Veakood muutus 27.3 ja 27.4 |
Rööpa valmistamise tehnoloogia rikkumisel võivad rööpapeadesse tekkida piki- või põikipraod. | Seda juhtub nii liigeses kui ka väljaspool seda | Kahjukood 30.1 või 30.2 |
Raudtee defektide tuvastamine
Tänapäeval on ultraheli meetod ainuke meetod, mis võimaldab raudteerööbaste uusi defekte varakult avastada ja seda ennetada.
See mittepurustav katsemeetod võib ultraheliimpulsside abil tuvastada metallrööbaste kahjustusi. Seda meetodit kasutatakse paljudes tööstusharudes, kus on tööd metalliga, kuid kõige populaarsem on see raudteejaamades, kus on kõige olulisem jälgida rööbaste kvaliteeti. Ultraheli vigade tuvastamine võimaldab töötajatel kiiresti ja täpselt tuvastada varjatud kahjustused, mõjutamata ega hävitamata samas uurimisobjekti.
Sellel rööbaste defektide tuvastamise meetodil on mitmeid vaieldamatuid eeliseid.
Esiteks ja kõige tähtsam on see, et katsekehale pole jäetud kahjustusi ega muid jälgi, st uusi defekte. Teiseks on selliste seadmete maksumus üsna madal ja nende kasutamise tulemusena saadud andmete usaldusväärsus on väga kõrge. Pealegi on see piisav alt olulineselline seade võimaldab otsida uusi rööpavigu igal aastaajal, mis on eriti oluline.
Ultraheli meetod defektide tuvastamiseks võimaldab teil leida isegi väikseimad kahjustused mis tahes metalltoodetest ja liitekohtadest. Seetõttu kasutatakse neid aktiivselt ka pöörete ja konstruktsiooni keevisõmbluste kontrollimiseks. Ultraheliseadmete abil saab määrata järgmisi kahjustusi: struktuuri homogeensuse rikkumiste esinemine; kontrollige korrosioonikahjustusega kohti; kontrollige, kas rööpa keemiline koostis vastab dokumentides märgitule või mitte.
Soovitan:
Konfliktid meeskonnas: nende lahendamise viisid, klassifikatsioon, põhjused ja tõhusad meetodid probleemide lahendamiseks
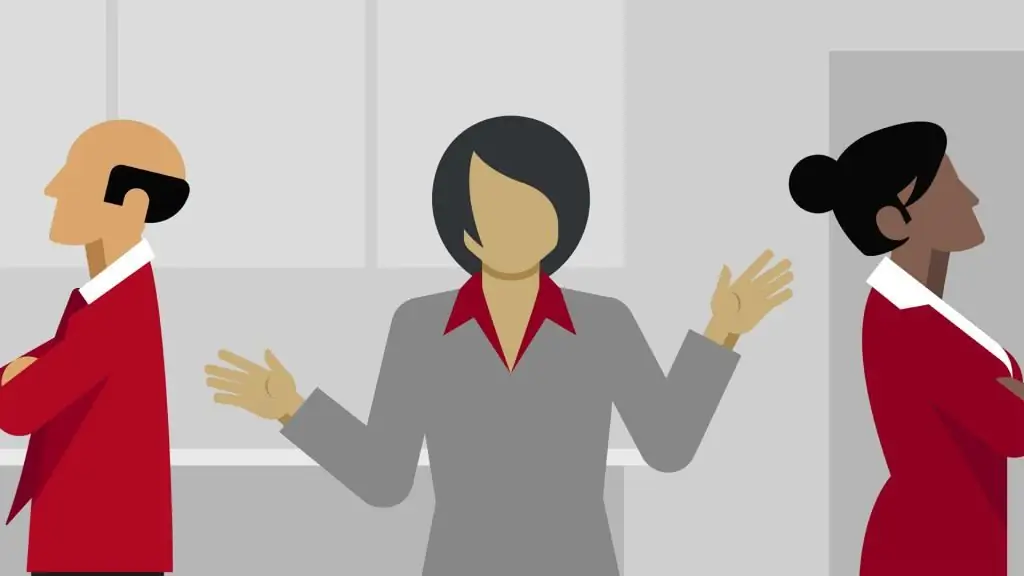
Meeskonnas tekkivate konfliktide probleem ja nende lahendamise viisid on aktuaalsed erinevate valdkondade ja valdkondadega seotud inimeste jaoks. Isiku eripäraks on teiste isikutega suhtlemise keerukus teatud tingimustel. Mida suurem on meeskond, seda suurem on tingimuste tekkimise tõenäosus, millele järgnevad pingelised konfliktsuhted. Vaatleme seda teemat üksikasjalikum alt
Mootorite klassifikatsioon. Mootorite tüübid, nende eesmärk, seade ja tööpõhimõte
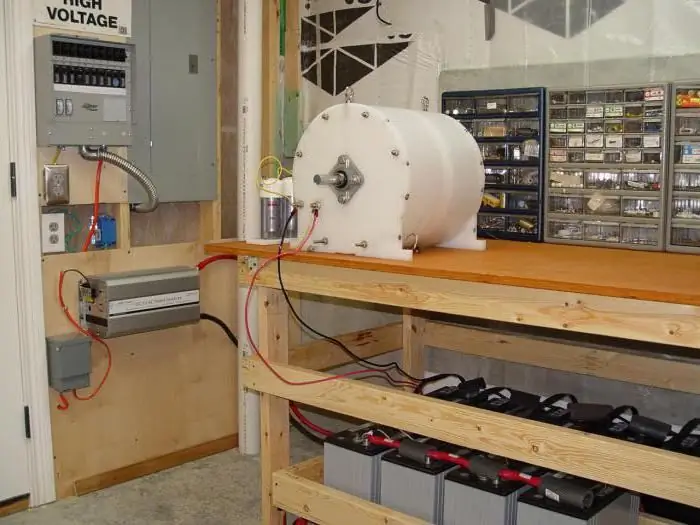
Tänapäeval töötab enamikul sõidukitel mootor. Selle seadme klassifikatsioon on tohutu ja sisaldab suurt hulka erinevat tüüpi mootoreid
Oksjonite tüübid, nende klassifikatsioon, omadused ja tingimused
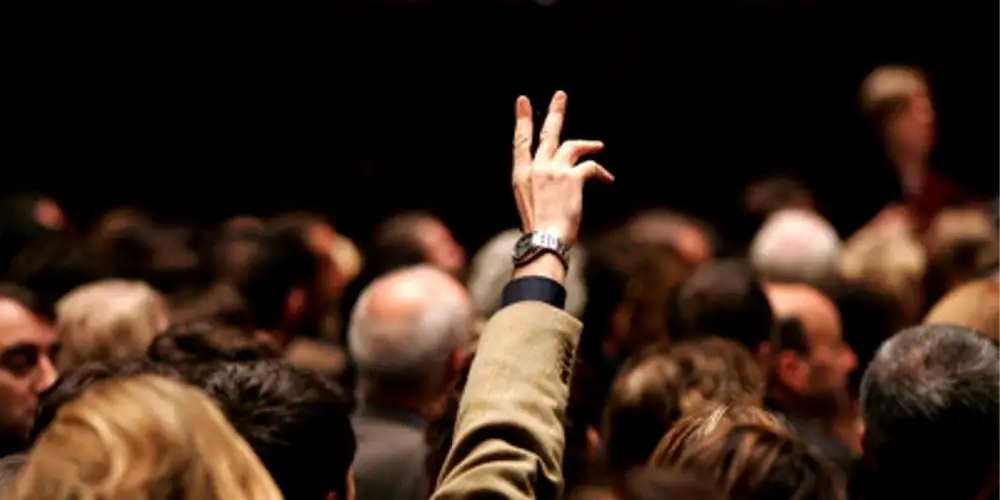
Mis on oksjon, mis tüüpi oksjoneid on olemas. Kuidas osaleda? Millised on reeglid? Kas on võimalik ostust keelduda ja mis sellest edasi saab? Proovime selle välja mõelda
Pankade reservid ja nende moodustamine. Panga kohustuslikud reservid ja nende norm
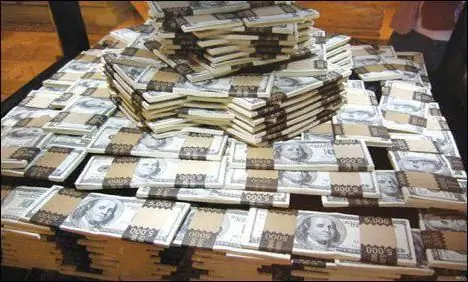
Pangareservid tagavad vahendite olemasolu hoiuste tagastamise ja teiste finantsasutustega arvelduste maksekohustuste katkematuks täitmiseks. Teisisõnu toimivad need garantiina
Leiva defektid: fotod, põhjused, küpsetusprobleemid ja nende parandamine
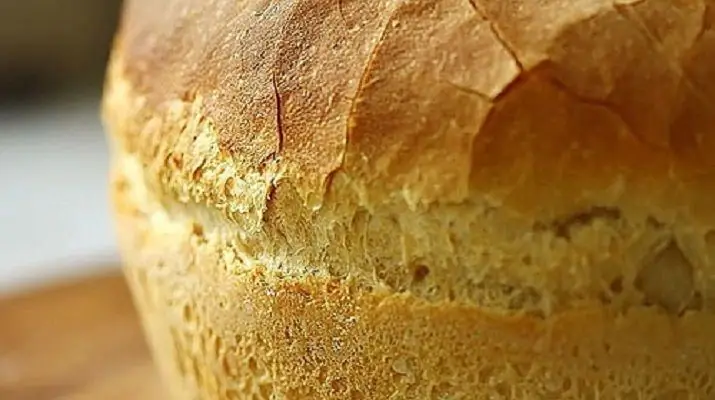
Leiva valmistamine on keeruline tehnoloogiline protsess. Pole üllatav, et valmis pagaritoodetel võib olla mitmesuguseid defekte. Nende põhjuseks võivad olla tooraine kehv kvaliteet, tainast sõtkuva ja küpsetava pagari vead. Väärib märkimist, et koostisosade kvaliteediga seotud vigu on äärmiselt raske parandada, samas kui tehnoloogilisi vigu saab parandada. Artiklis räägitakse leiva defektidest ja nende kõrvaldamisest