2025 Autor: Howard Calhoun | [email protected]. Viimati modifitseeritud: 2025-06-01 07:13
Kõrgtugevate teraste saamise protsessides mängivad olulist rolli legeerimistoimingud ja põhikoostise muutmine. Selliste protseduuride aluseks on erinevate omadustega metallilisandite lisamise tehnika, kuid väikese tähtsusega pole ka gaasi-õhu reguleerimine. Just sellele tehnoloogilisele toimingule on orienteeritud metallurgias terassulamite suurtes kogustes tootmisel laialdaselt kasutatava hapnikukonverteri töö.
Konverteri disain
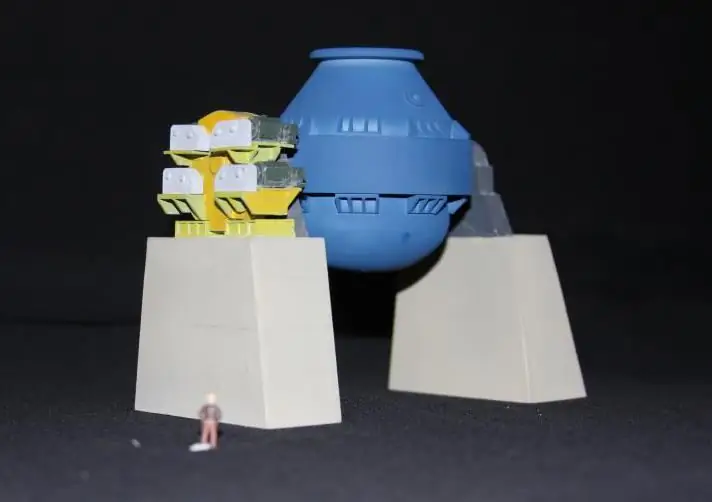
Seade on pirnikujuline anum, mis on varustatud sisevooderdusega ja kraaniavaga sulatustoodete vabastamiseks. Konstruktsiooni ülaosas on kaelaga ava toru, vanaraua, sularaua, legeerivate segude ja gaasi eemaldamiseks. Tonnaaž varieerub 50-400 tonni Konstruktsiooni valmistamisel kasutatakse materjalidena leht- või keevitatud keskterast.paksus umbes 50-70 mm. Tüüpiline hapnikukonverteri seade annab võimaluse põhja lahti võtta - need on modifikatsioonid põhjapuhastusega gaasi-õhu segudega. Seadme abi- ja funktsionaalsetest elementidest võib välja tuua elektrimootori, hapnikuvoolude tsirkulatsioonitorustiku infrastruktuuri, tõukelaagrid, siibriplatvormi ja tugiraami konstruktsiooni paigaldamiseks.
Tugirõngad ja tugirõngad
Muundur asub rull-laagritel, mis on kinnitatud raami külge. Disain võib olla statsionaarne, kuid see on haruldane. Tavaliselt määratakse projekteerimisetappides seadme transportimise või teisaldamise võimalus teatud tingimustel. Nende funktsioonide eest vastutavad tugirõngaste ja tihvtide kujul olevad seadmed. Laagrite rühm annab võimaluse seadmete väändumiseks ümber võllide telje. Varasemad muundurite mudelid eeldasid kandeseadme ja sulatusseadme korpuse kombinatsiooni, kuid kõrgete temperatuuride ja abimaterjalide deformatsiooni tõttu asendati see konstruktsioonilahendus keerukama, kuid usaldusväärse ja vastupidava interaktsiooniskeemiga. funktsionaalne üksus ja veresoon.
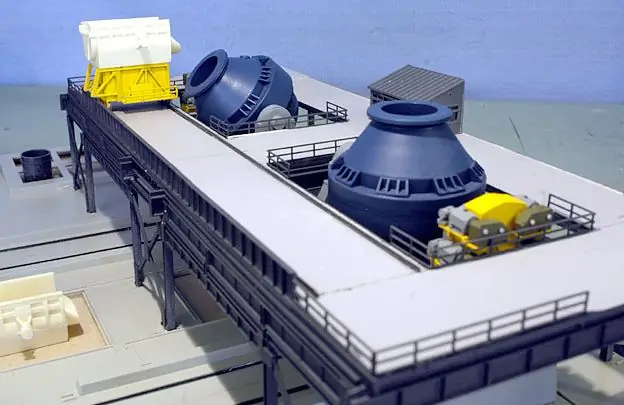
Eelkõige on tänapäevane hapnikumuundur varustatud eraldi tugirõngaga, mille konstruktsiooni on sisse viidud ka rõngad ja fikseeritud korpus. Tehnoloogiline vahe korpuse ja tugialuse vahel hoiab ära negatiivse temperatuuri mõju vedrustuse ja liikuvate mehhanismide tundlikele elementidele. Konverteri enda kinnitussüsteem on realiseeritud peatustega. Tugirõngas ise on kandja, mis on moodustatud kahest poolrõngast ja dokkimispunktidesse kinnitatud haruplaatidest.
Pöördmehhanism
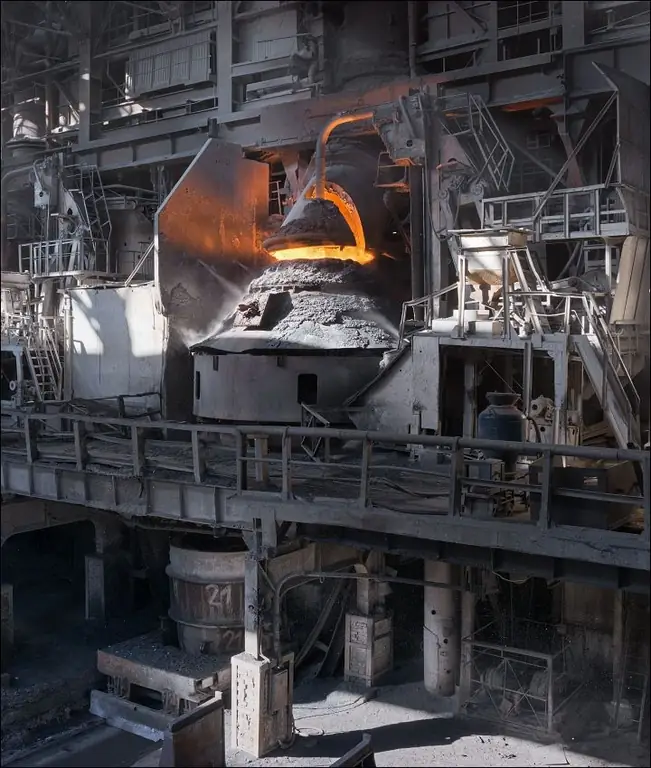
Elektriline ajam võimaldab muunduril 360° pöörata. Keskmine pöörlemiskiirus on 0,1-1 m/min. Iseenesest pole see funktsioon alati vajalik - olenev alt tehnoloogiliste toimingute korraldusest töövoo ajal. Näiteks võib osutuda vajalikuks pööre, et suunata kael otse vanaraua tarnimise, raua valamise, terase äravoolu jne kohta. Pööramismehhanismi funktsionaalsus võib olla erinev. On nii ühesuunalisi kui ka kahesuunalisi süsteeme. Reeglina võtavad kuni 200 tonnise kandevõimega hapnikumuundurid pöörde ainult ühes suunas. See on tingitud asjaolust, et sellistes konstruktsioonides on kaela kallutamisel vaja vähem pöördemomenti. Üleliigse energiatarbimise välistamiseks raskeveokite töötamise ajal on see varustatud kahesuunalise pöörlemismehhanismiga, mis kompenseerib kaelaga manipuleerimise kulud. Torsioonsüsteemi struktuur sisaldab käigukasti, elektrimootorit ja spindlit. See on betoonpõrandale paigaldatud statsionaarse ajami traditsiooniline paigutus. Tehnoloogilisemad liigendiga mehhanismid on kinnitatud võlli külge ja neid juhib laagrisüsteemiga ajam, mida käivitavad ka elektrimootorid võllisüsteemi kaudu.
Konverteri mõõtmed
Projekteerimise käigus tuleb projekteerimisparameetrid arvutada selle põhjal, milline ligikaudne puhastusmaht, välja arvatud sulatise väljutamine, toodetakse. Viimastel aastatel on välja töötatud agregaadid, mis võtavad vastu materjale mahus 1 kuni 0,85 m3/t. Arvutatakse ka kurgu kalle, mille kaldenurk on keskmiselt 20° kuni 35°. Kuid selliste rajatiste käitamise praktika näitab, et 26° kalde ületamine halvendab voodri kvaliteeti. Sügavuses on muunduri mõõtmed 1-2 m, kuid kandevõime kasvades võib suureneda ka konstruktsiooni kõrgus. Tavalised kuni 1 m sügavused muundurid taluvad koormust kuni 50 tonni. Mis puudutab läbimõõtu, siis see varieerub keskmiselt 4-7 m. Kaela paksus on 2-2,5 m.
BOF vooder
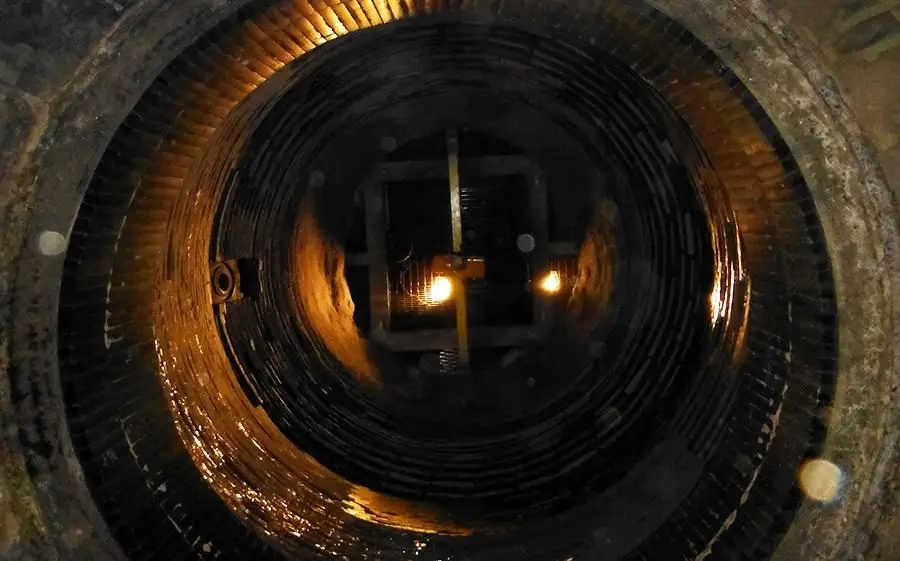
Kohustuslik tehnoloogiline protseduur, mille käigus muunduri siseseinad varustatakse kaitsekihiga. Samal ajal tuleb arvestada, et erinev alt enamikust metallurgiaahjudest on sellel konstruktsioonil palju suurem soojuskoormus, mis määrab ka voodri omadused. See on protseduur, mis hõlmab kahe kaitsekihi - funktsionaalse ja tugevdava - paigaldamist. Otse kere pinnaga külgneb 100-250 mm paksune kaitsetugevduskiht. Selle ülesanne on vähendada soojuskadusid ja vältida ülemise kihi läbipõlemist. Materjaliks on magnesiit või magnesiit-kromiit tellis, mis võib ilma uuendamiseta töötada aastaid.
Peamine töökiht on umbes 500-700 mm paksune ja seda vahetatakse kulumisel üsna sageli välja. Selles etapis töödeldakse BOF-i mittepõlevate liiva või vaiguga seotud tulekindlate ühenditega. Selle voodrikihi alusmaterjaliks on magnesiidilisanditega dolomiit. Standardkoormuse arvutus põhineb temperatuuri mõjul umbes 100-500 °C.
Shotcrete vooder
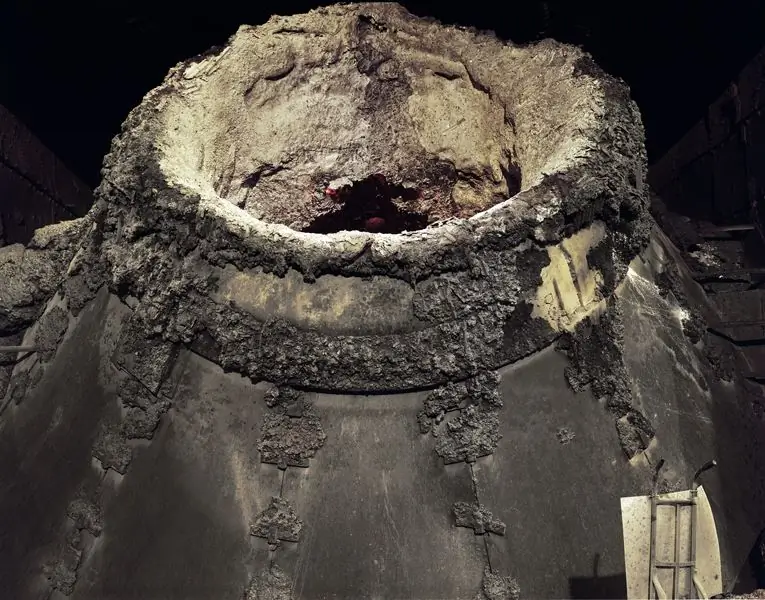
Agressiivse temperatuuri ja keemiliste mõjude mõjul kaotavad muunduri struktuuri sisepinnad kiiresti oma omadused - see puudutab jällegi termokaitse töökihi välist kulumist. Remonditöödena kasutatakse toorbetoonvooderdust. See on kuumredutseerimistehnoloogia, mille käigus paigaldatakse spetsiaalse varustuse abil tulekindel kompositsioon. Seda kantakse mitte pidev alt, vaid punktsuunas alusvoodri tugev alt kulunud kohtadele. Protseduur viiakse läbi spetsiaalsetel haavelbetoonmasinatel, mis toidavad kahjustatud piirkonda koksitolmu ja magnesiidipulbri massiga vesijahutusega toru.
Sulamistehnoloogiad
Traditsiooniliselt on hapnikumuunduri sulatamise rakendamisel kaks lähenemisviisi - Bessemer ja Thomas. Kaasaegsed meetodid erinevad neist aga madala lämmastikusisalduse poolest ahjus, mis parandab tööprotsessi kvaliteeti. Tehnoloogiat rakendatakse järgmistes etappides:
- Sirmi laadimine. Umbes 25-27% laengu kogumassist laaditakse kulbide abil kaldmuundurisse.
- Täitminemalmist või terasesulam. Vedel metall temperatuuril kuni 1450 °C valatakse kulpide abil kaldkonverterisse. Toiming ei kesta üle 3 minuti.
- Puhastus. Selles osas võimaldab hapnikukonverterites terase valmistamise tehnoloogia erinevaid lähenemisviise gaasi-õhu segu varustamisel. Voolu saab suunata ül alt, alt, alt ja kombineeritud viisil, olenev alt seadme konstruktsiooni tüübist.
- Näidiste vastuvõtmine. Mõõdetakse temperatuur, eemaldatakse soovimatud lisandid ja oodatakse koostise analüüsi. Kui selle tulemused vastavad konstruktsiooninõuetele, siis sulatis vabastatakse ja kui mitte, tehakse muudatusi.
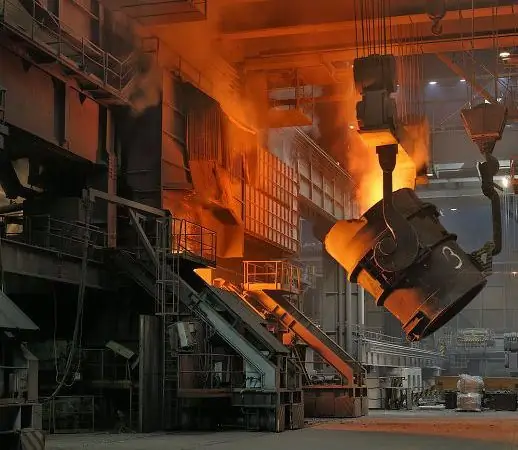
Tehnoloogia plussid ja miinused
Meetodit hinnatakse selle kõrge tootlikkuse, lihtsate hapnikuvarustusskeemide, struktuurilise töökindluse ja üldiselt suhteliselt madalate kulude tõttu protsessi korraldamisel. Mis puudutab miinuseid, siis need hõlmavad eelkõige piiranguid muda ja taaskasutatavate materjalide lisamisel. Sama vanametalli koos muude lisanditega ei tohi olla rohkem kui 10% ja see ei võimalda sulatuskonstruktsiooni vajalikul määral muuta. Lisaks kulub puhumisel palju kasulikku rauda.
Tehnoloogia rakendamine
Plusside ja miinuste kombinatsioon määras lõppkokkuvõttes muundurite kasutamise olemuse. Eelkõige toodavad metallurgiatehased kõrge kvaliteediga madala legeeritud, süsinikusisaldusega ja legeerterast, millest piisab materjali kasutamiseks rasketööstuses ja ehituses. Teraste vastuvõtminehapnikumuundur on legeeritud ja täiustatud individuaalsed omadused, mis laiendab lõpptoote ulatust. Saadud toorainest valmistatakse torud, traat, rööpad, riistvara, riistvara jne. Tehnoloogiat kasutatakse laialdaselt ka värvilises metallurgias, kus piisava puhumisega saadakse mullvask.
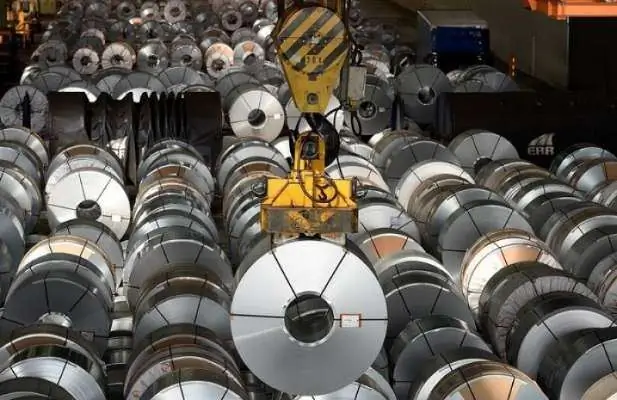
Järeldus
Konverteriseadmetes sulatamist peetakse moraalselt vananenud tehnikaks, kuid seda kasutatakse jätkuv alt protsessi tootlikkuse ja finantskulude optimaalse kombinatsiooni tõttu. Suurel määral soodustavad tehnoloogia nõudlust ka kasutatavate seadmete struktuursed eelised. Sama võimalus metallijäätmete, laengu, muda ja muude jäätmete otselaadimiseks, kuigi piiratud ulatuses, avardab sulami muutmise võimalusi. Teine asi on see, et suurte, pööramisvõimeliste muundurite täieõiguslikuks tööks on vaja ettevõttes sobiva ruumi korraldamist. Seetõttu teostavad suurtes kogustes hapnikupuhastusega sulatamist peamiselt suured ettevõtted.
Soovitan:
Terase katmine titaannitriidiga. Pulbri tehnoloogia
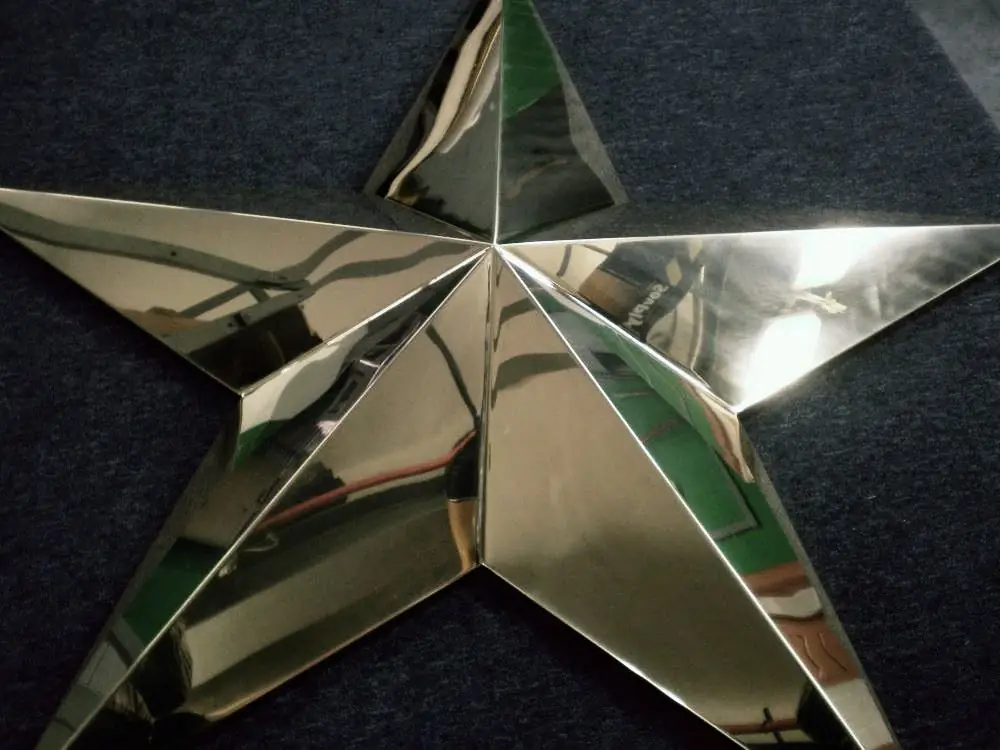
Meie aja materjalide katmiseks kasutatakse tervet rida erinevaid tehnoloogiaid. On olemas vaakumkatte tehnoloogiad, elektron-prootonkiirgus, kõrgtemperatuuriline süntees ja palju muud. Kaasaegses maailmas muutuvad üha populaarsemaks "kullatud" dekoratiivsed kaunistused ja tooted
Toidu roostevaba teras: GOST. Kuidas teha kindlaks toidukvaliteediga roostevaba teras? Mis vahe on toiduainete roostevaba terase ja tehnilise roostevaba terase vahel?

Artikkel räägib toidukvaliteediga roostevaba terase klassidest. Lugege, kuidas eristada toiduainete roostevaba terast tehnilisest
Joodis vase, alumiiniumi, messingi, terase ja roostevaba terase jootmiseks. Jootekompositsioon jootmiseks. Joodiste tüübid jootmiseks
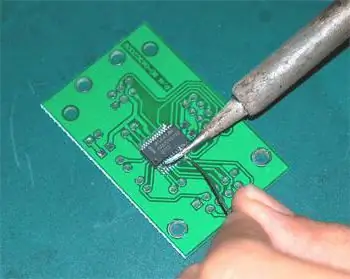
Kui on vaja erinevaid tahkeid liitekohti omavahel kindl alt kinnitada, valitakse selleks kõige sagedamini jootmine. See protsess on paljudes tööstusharudes lai alt levinud. Peame jootma ja kodukäsitöölisi
Külmsuitsutamise tehnoloogia: protsessi kontseptsioon, suitsuahju ehitus, suitsetamise ja toidu valmistamise peamised reeglid
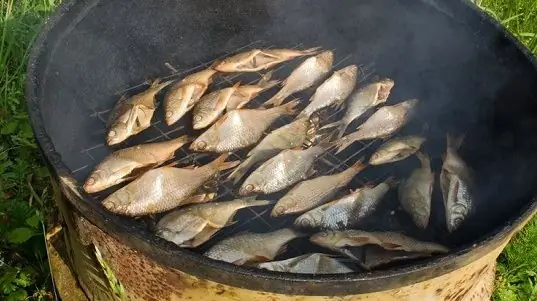
Maal kala või liha küpsetamisel saab soovi korral kasutada ka külmsuitsutamistehnoloogiat. Seda tehnikat kasutades pole väga maitsva omatehtud toote saamine keeruline. Küll aga kala, liha või vorsti suitsutamiseks tuleb seda muidugi õigesti teha
Terase lõõmutamine kui kuumtöötluse liik. Metalli tehnoloogia
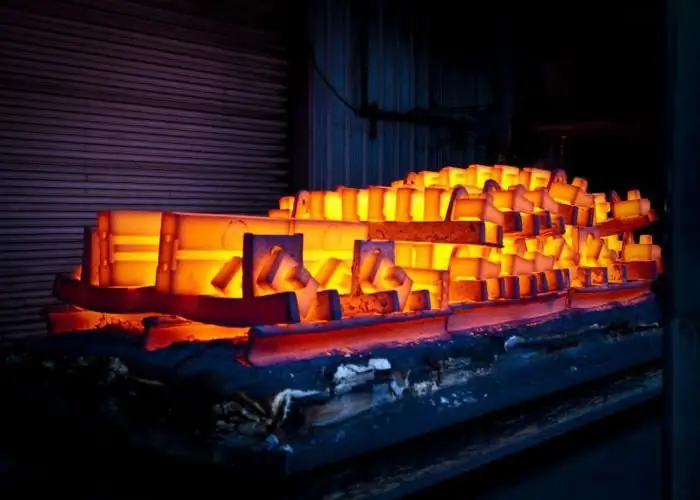
Uute materjalide loomine ja nende omaduste kontrollimine on metallitehnoloogia kunst. Üks selle tööriistu on kuumtöötlus. Need teadmised võimaldavad teil muuta sulamite omadusi ja vastav alt ka kasutusvaldkondi. Terase lõõmutamine on laialdaselt kasutatav võimalus toodete tootmisdefektide kõrvaldamiseks, nende tugevuse ja töökindluse suurendamiseks