2025 Autor: Howard Calhoun | [email protected]. Viimati modifitseeritud: 2025-06-01 07:13
Tänu kergusele, plastilisusele ja korrosioonikindlusele on alumiiniumist saanud paljudes tööstusharudes asendamatu materjal. Lennualumiinium on sulamite rühm, mida iseloomustab suurenenud tugevus magneesiumi, räni, vase ja mangaani lisamisega. Lisatugevust antakse sulamile nn. "vananemisefekt" - spetsiaalne kõvenemise meetod agressiivse atmosfäärikeskkonna mõjul pikka aega. Sulam leiutati 20. sajandi alguses, seda nimetatakse duralumiiniumiks, mida praegu tuntakse ka kui "aviaali".
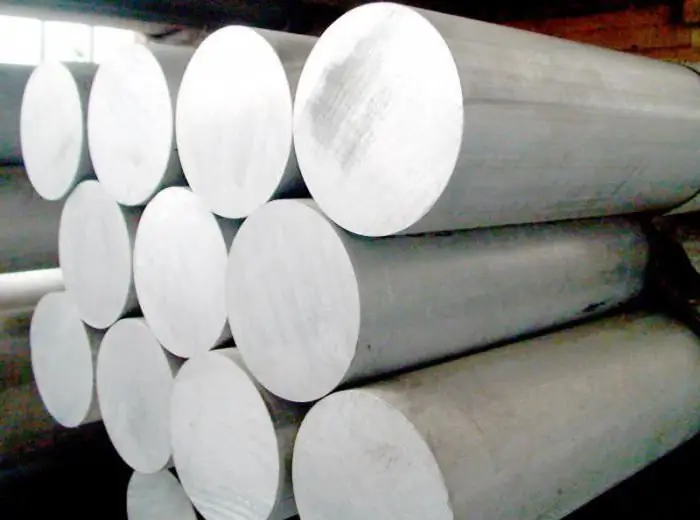
Definitsioon. Ajalooline ekskursioon
Lennunduse alumiiniumsulamite ajaloo alguseks peetakse 1909. aastat. Saksa metallurgiainsener Alfred Wilm tegi eksperimentaalselt kindlaks, et kui alumiiniumisulamit, millele on lisatud veidi vaske, mangaani ja magneesiumi, hoitakse pärast jahutamist temperatuuril 500 ° C ja kiiret jahutamist temperatuuril 20-25 kraadi 4-5 päeva., muutub see järk-järgult kõvemaks ja tugevamaks, kaotamata elastsust. Protseduuri nimetati "vananemiseks" või "küpsemiseks". Sellise kõvenemise käigus täituvad vaseaatomidpalju pisikesi tsoone teravilja piiridel. Vase aatomi läbimõõt on väiksem kui alumiiniumil, seetõttu tekib survepinge, mille tulemusena suureneb materjali tugevus.
Esimest korda meisterdati sulam Saksa tehastes Dürener Metallwerken ja sai kaubamärgi Dural, sellest ka nimetus "duralumiinium". Seejärel parandasid Ameerika metallurgid R. Archer ja V. Jafris koostist, muutes peamiselt magneesiumi protsenti. Uus sulam sai nimeks 2024, mis on praegugi laialdaselt kasutusel erinevates modifikatsioonides ning kogu sulamite perekond kannab nime Avial. See sulam sai nimetuse "lennunduse alumiinium" peaaegu kohe pärast selle avastamist, kuna see asendas täielikult puidu ja metalli lennukikonstruktsioonides.
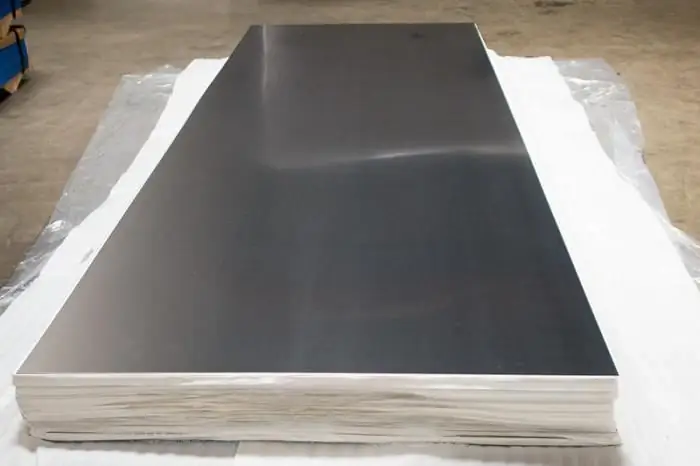
Peamised tüübid ja omadused
Seal on kolm põhirühma:
- Alumiinium-mangaani (Al-Mn) ja alumiinium-magneesiumi (Al-Mg) perekonnad. Peamine omadus on kõrge korrosioonikindlus, mis on vaevu halvem kui puhas alumiinium. Sellised sulamid sobivad hästi jootmiseks ja keevitamiseks, kuid on halvasti lõigatud. Ei ole kuumtöötlemisel kõvastunud.
- Alumiiniumi-magneesiumi-räni (Al-Mg-Si) süsteemi korrosioonikindlad sulamid. Need kõvenevad kuumtöötlemise teel, nimelt kõvenemisega temperatuuril 520 °C, millele järgneb kiire veega jahutamine ja loomulik vananemine umbes 10 päeva. Selle materjalirühma eripäraks on nende kõrge korrosioonikindlus tavatingimustes ja pinge all töötamisel.
- Struktuursed alumiiniumi-vase-magneesiumi sulamid (Al-Cu-Mg). Nende aluseks on vase, mangaani ja magneesiumiga legeeritud alumiinium. Legeerelementide proportsioonide muutmisega saadakse lennukiklassi alumiinium, mille omadused võivad erineda.
Viimase rühma materjalidel on head mehaanilised omadused, kuid need on väga vastuvõtlikud korrosioonile kui esimese ja teise rühma sulamid. Korrosioonitundlikkuse aste sõltub pinnatöötluse tüübist, mida tuleb veel kaitsta värvi või anodeerimisega. Korrosioonikindlust suurendab osaliselt mangaani lisamine sulami koostisse.
Lisaks kolmele peamisele sulamitüübile on olemas ka sepistamissulamid, kuumakindlad, ülitugevad konstruktsiooni- ja muud sulamid, millel on konkreetse rakenduse jaoks vajalikud omadused.
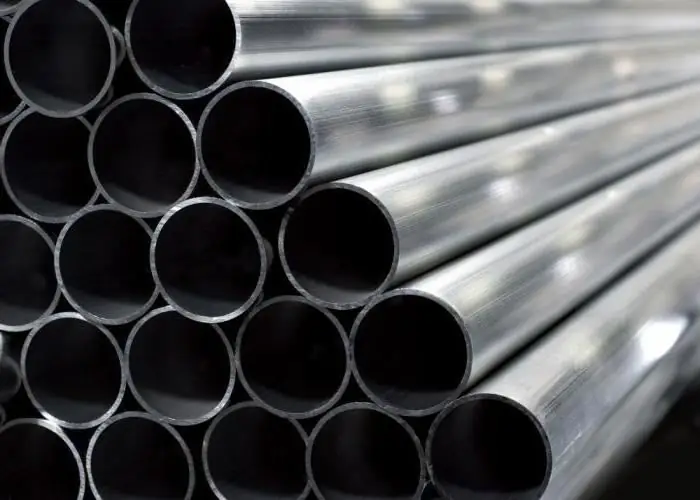
Lennundussulamite märgistamine
Rahvusvahelistes standardites näitab lennuki alumiiniumi märgistuse esimene number sulami peamisi legeerivaid elemente:
- 1000 - puhas alumiinium.
- 2000 - duralumiiniumid, vasega legeeritud sulamid. Teatud perioodil - kõige levinum kosmosesulam. Üha enam asendatakse 7000-seeria sulamitega, kuna need on väga vastuvõtlikud pingekorrosioonipragunemisele.
- 3000 - legeerelement - mangaan.
- 4000 - legeerelement - räni. Sulameid tuntakse ka silumiinidena.
- 5000 - legeerelement - magneesium.
- 6000 on kõige plastilisemad sulamid. Legeerivad elemendid on magneesium ja räni. Tugevuse suurendamiseks võib kuumkarastada, kuid seeparameeter on madalam kui seeriatel 2000 ja 7000.
- 7000 - termiliselt karastatud sulamid, kõige vastupidavam lennukialumiinium. Peamised legeerivad elemendid on tsink ja magneesium.
Märgistuse teine number on alumiiniumisulami modifikatsiooni seerianumber pärast originaali - number "0". Kaks viimast numbrit on sulami enda number, teave selle puhtuse kohta lisandite järgi. Kui sulam on kogenud, lisatakse märgistusele viies "X".
Tänapäeval on kõige levinumad lennukialumiiniumi klassid: 1100, 2014, 2017, 3003, 2024, 2219, 2025, 5052, 5056. Nende sulamite iseloomulikud tunnused on: kergus, elastsus, hea hõõrdetugevus, korrosioon ja suured koormused. Lennukitööstuses on enim kasutatud sulamid 6061 ja 7075 lennukialumiinium.
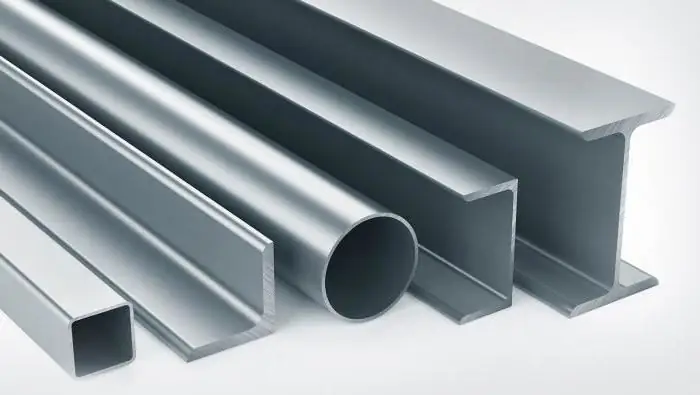
Kompositsioon
Lennualumiiniumi peamised legeerivad elemendid on: vask, magneesium, räni, mangaan, tsink. Nende elementide massiprotsenti sulamis määravad sellised omadused nagu tugevus, painduvus, vastupidavus mehaanilisele pingele jne. Sulami alus on alumiinium, peamisteks legeerivateks elementideks on vask (2,2-5,2 massiprotsenti). magneesium (0,2-2,7%) ja mangaan (0,2-1%).
Räniga (4-13 massiprotsenti) valmistatud alumiiniumisulamite perekond, milles on vähe muid legeerivaid elemente - vask, mangaan, magneesium, tsink, titaan, berüllium. Kasutatakse keeruliste osade valmistamiseks, tuntud ka kui silumiin või valatud alumiiniumsulam. alumiinium-magneesiumisulamite perekond(1-13% massist) koos teiste elementidega on kõrge plastilisuse ja korrosioonikindlusega.
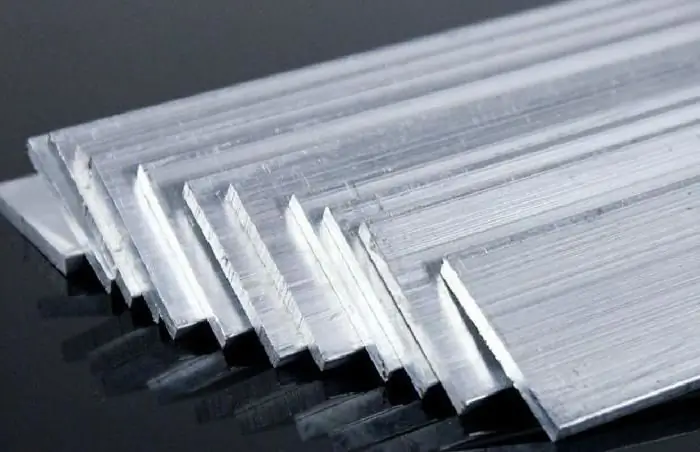
Vase roll lennukialumiiniumis
Vase sisaldus lennukisulami koostises aitab kaasa selle kõvenemisele, kuid mõjub samal ajal halvasti selle korrosioonikindlusele. Karastusprotsessi ajal tera piiridel välja langenud vask muudab sulami tundlikuks täppkorrosioonile, pingekorrosioonile ja teradevahelisele korrosioonile. Vaserikkad alad on galvaaniliselt katoodsemad kui ümbritsev alumiiniummaatriks ja seetõttu tundlikumad galvaanilise korrosiooni suhtes. Vasesisalduse suurenemine sulami massis kuni 12% suurendab tugevusomadusi tänu dispersiooni tugevnemisele vananemise ajal. Kui vasesisaldus on üle 12%, muutub sulam rabedaks.
Kasutusvaldkonnad
Alumiiniumsulamid on müügil kõige nõutum metall. Lennukikvaliteediga alumiiniumi kerge kaal ja selle tugevus teevad sellest sulamist hea valiku paljudes tööstusharudes alates lennukitest kuni majapidamistarveteni (mobiiltelefonid, kõrvaklapid, taskulambid). Alumiiniumsulameid kasutatakse laevaehituses, autotööstuses, ehituses, raudteetranspordis ja tuumatööstuses.
Mõõduka vasesisaldusega sulamid on lai alt nõutud (2014, 2024 jne). Nendest sulamitest valmistatud profiilidel on kõrge korrosioonikindlus, hea töödeldavus ja punktkeevitatavus. Neid kasutatakse õhusõidukite, raskete sõidukite ja sõjavarustuse kriitiliste struktuuride valmistamiseks.
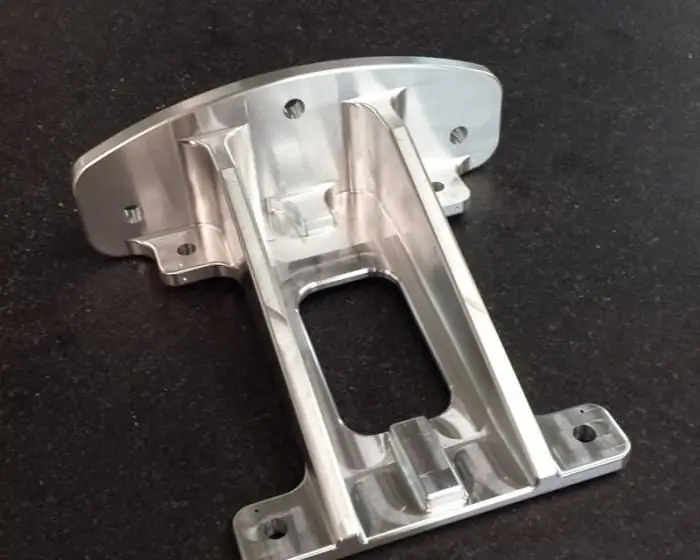
Lennukiklassi alumiiniumist ühendusfunktsioonid
Lennukisulamite keevitamine toimub eranditult inertgaaside kaitsvas keskkonnas. Eelistatavad gaasid on: heelium, argoon või nende segu. Heeliumil on kõrgem soojusjuhtivus. See määrab keevituskeskkonna soodsamad temperatuurinäitajad, mis võimaldab paksuseinalisi konstruktsioonielemente üsna mugav alt ühendada. Kaitsegaaside segu kasutamine aitab kaasa gaasi täielikumale eemaldamisele. Sel juhul väheneb oluliselt pooride tekkimise tõenäosus keevisõmbluses.
Lennukirakendused
Lennunduse alumiiniumsulamid loodi algselt spetsiaalselt lennundusseadmete ehitamiseks. Nendest valmistatakse lennuki kered, mootoriosad, šassiid, kütusepaagid, kinnitused jne. Salongi sisemuses on kasutatud lennunduse alumiiniumi detaile.
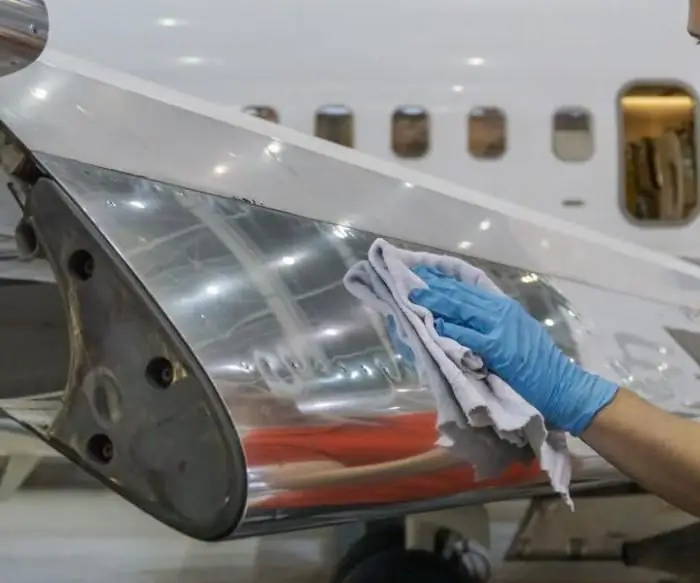
2xxx seeria alumiiniumsulameid kasutatakse kõrge temperatuuriga kokkupuutuvate osade tootmiseks. Kergelt koormatud agregaatide, kütuse-, hüdro- ja õlisüsteemide osad on valmistatud 3xxx, 5xxx ja 6xxx sulamitest. Lennukitööstuses on kõige laiemat rakendust leidnud sulam 7075. Sellest valmistatakse elemendid töötamiseks olulisel koormusel, madalatel temperatuuridel ja kõrge korrosioonikindlusega. Sulami aluseks on alumiinium ja peamised legeerivad elemendid on magneesium, tsink ja vask. Sellest valmistatakse lennukikonstruktsioonide võimsusprofiilid, nahaelemendid.
Soovitan:
Kasahhi valgepealine lehmatõug: omadused, omadused ja ülevaated
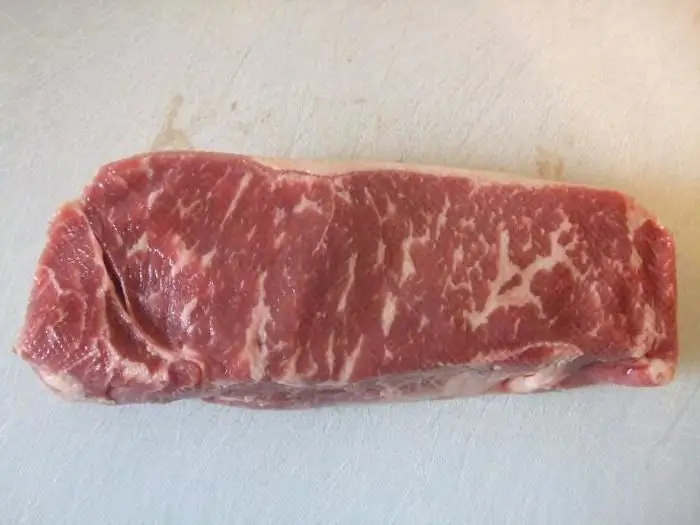
Kasahhi valgepealist lehmatõugu aretati NSV Liidus eelmise sajandi keskel. Selle vaieldamatute eeliste hulka kuulub liha kõrge tootlikkus, vähenõudlikkus sööda osas ja võime kiiresti kaalus juurde võtta kõige raskemates kliimatingimustes
Usinskoje valdkond: tehnoloogiate peamised omadused ja omadused
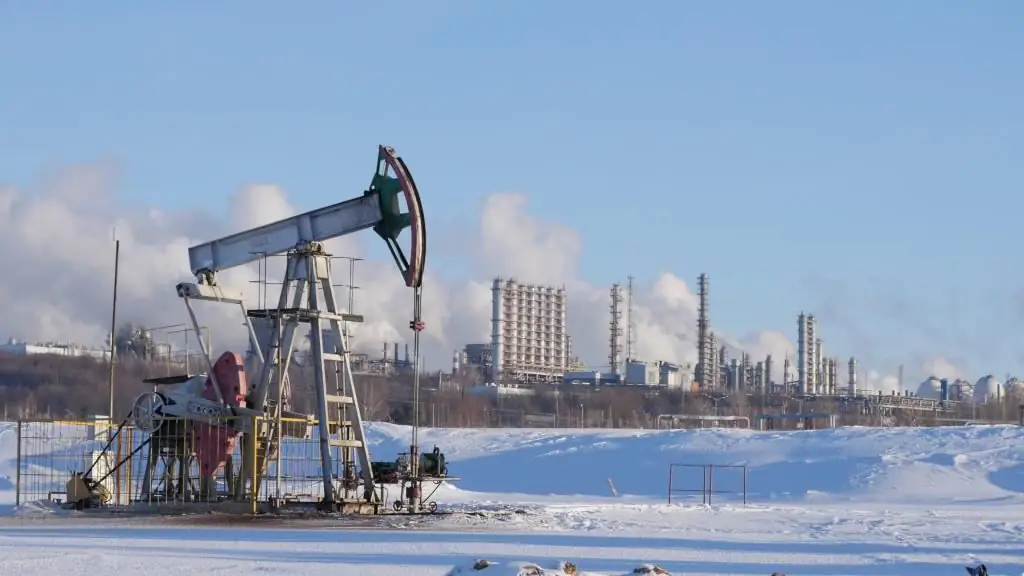
Usinskoje väli: geograafiline asukoht, kirjeldus, prognoositavad süsivesinike varud. Nafta omadused ja maardla geoloogiline struktuur. Maardla avastamise ja uurimise ajalugu. Õli tootmise tehnoloogia
Ideaalne juht: milline ta peaks olema, omadused ja omadused
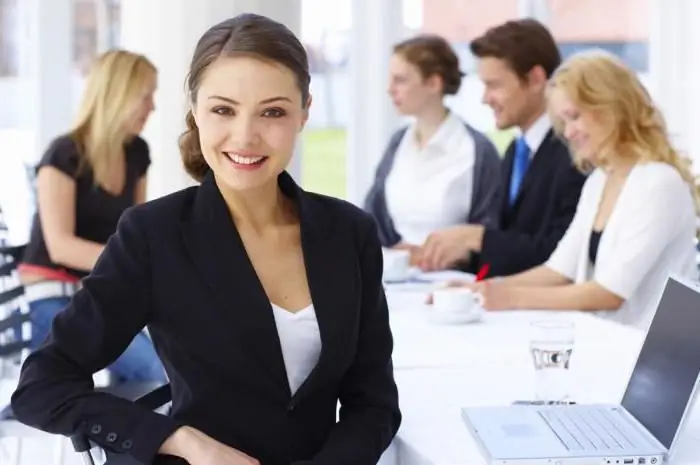
Millised omadused ja omadused peaksid ideaalsel juhil olema? Puuduvad ranged reeglid ja kriteeriumid, kuid on mitmeid omadusi, mida võib tõesti ülemuse jaoks kõige olulisemaks pidada
Teras 10HSND: omadused, omadused, koostis
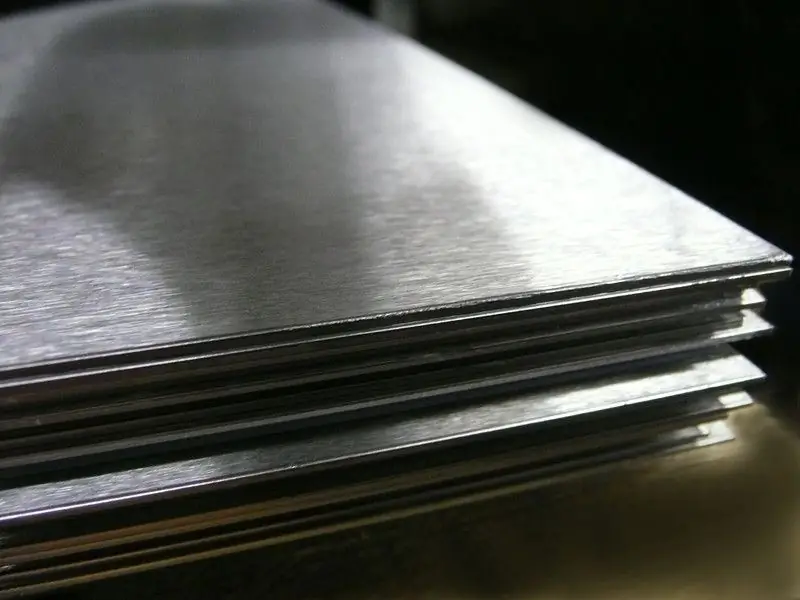
Mõnikord võib olla väga kasulik, kui teie silme ees on lühike väljavõte, mis sisaldab kogu kõige olulisemat teavet konkreetse probleemi kohta. See artikkel on selline väljavõte, mis sisaldab kogu kõige olulisemat teavet 10KhSND terase kohta: omadused, selle rakendus, koostis ja omadused
Teras C235: omadused, omadused, koostis
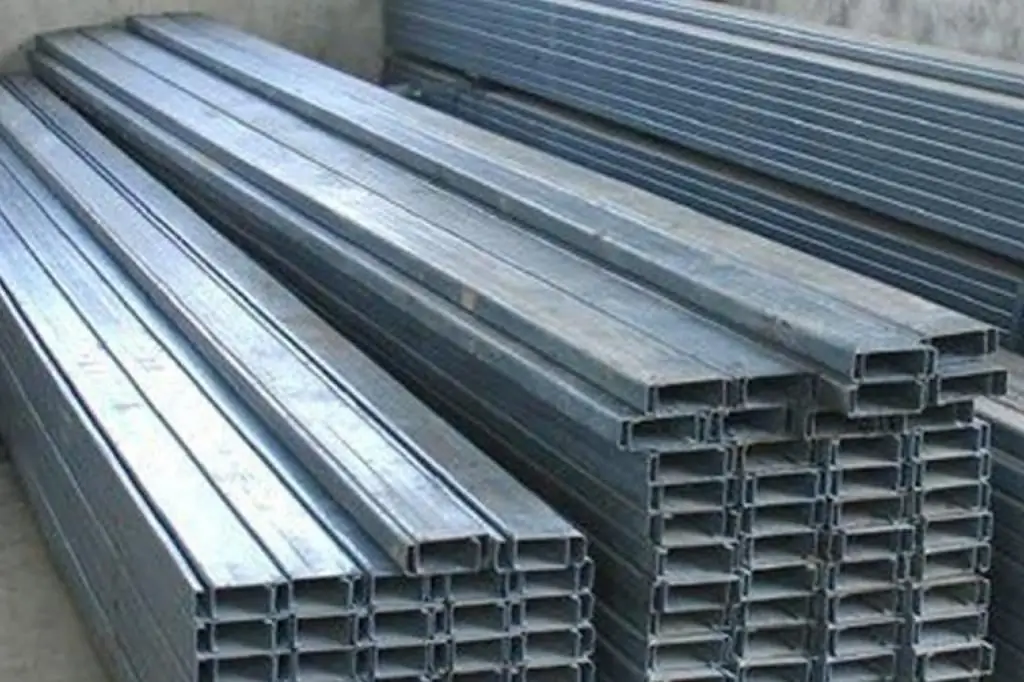
Tihti juhtub, et peate uurima suurt teabekihti ja nagu tavaliselt, pole palju aega. Sellises olukorras on sellised artiklid nagu käesolev väga kasulikud: informatiivsed ja sisutihedad. Näiteks sisaldab see lühike ülevaade kogu kõige vajalikumat teavet teraseklassi C235 kohta: selle koostis, omadused, analoogid, dekodeerimine ja ulatus. Olles seda uurinud, leiab igaüks vajadusel hõlpsasti vajaliku metallitüübi